Nut spot welding machines have gained significant popularity and widespread usage in various industries. In this article, we will explore the reasons behind the extensive use of nut spot welding machines. Understanding the advantages and benefits of these machines can provide valuable insights into their widespread adoption and application.
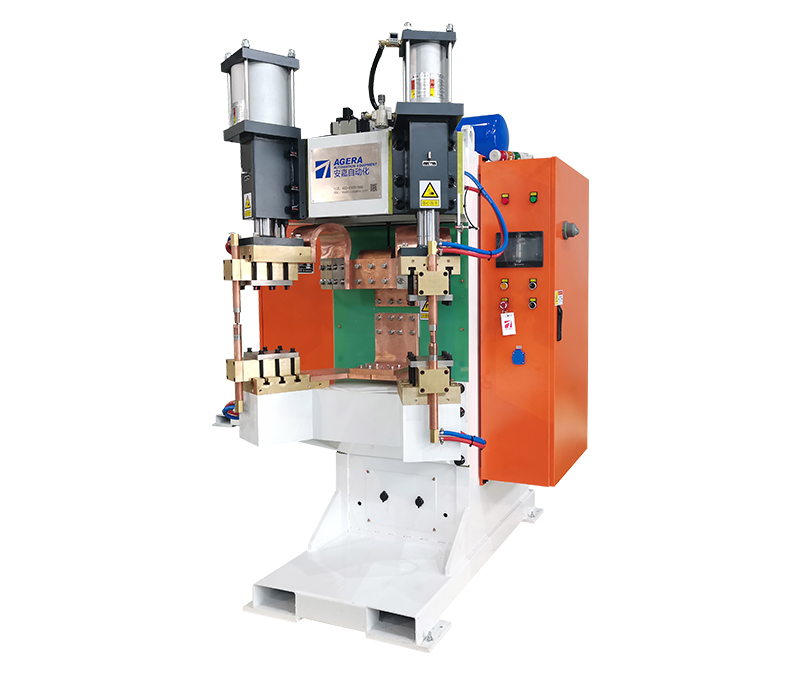
- Efficient and Time-Saving: Nut spot welding machines offer high efficiency and time-saving capabilities. By utilizing automated processes, these machines can rapidly join nuts to metal sheets or components. Compared to traditional welding methods, such as manual arc welding, nut spot welding machines significantly reduce the overall welding time, thereby enhancing productivity and throughput.
- Cost-Effective: Nut spot welding machines offer cost-effectiveness in terms of both equipment and operational expenses. The automated nature of these machines reduces the need for skilled labor, as they require minimal manual intervention. Additionally, the precise control and repeatability of the welding process minimize material waste and rework, resulting in cost savings for manufacturers.
- High Welding Strength: Nut spot welding machines produce welds with high strength and integrity. The localized heating and compression of the joint during the welding process create robust connections. These welds exhibit excellent resistance to shear and tensile forces, making them suitable for applications requiring secure fastening and structural integrity.
- Versatility: Nut spot welding machines offer versatility in terms of the range of materials they can weld. They can effectively join nuts to various metal sheets, including steel, aluminum, and stainless steel. This versatility enables their use in a wide range of industries, such as automotive, aerospace, electronics, and construction.
- Consistency and Quality Control: Nut spot welding machines provide consistent and repeatable welds, ensuring high-quality joints. The automated process eliminates operator-dependent variations, resulting in uniform weld quality throughout production. Additionally, these machines often incorporate monitoring and control systems to detect and prevent welding defects, further enhancing the overall quality of the welds.
- Space-Saving Design: Nut spot welding machines are typically compact and space-saving in design. They require a relatively small footprint, making them suitable for both large-scale manufacturing facilities and smaller workshop environments. Their compact size allows for easy integration into existing production lines or workstations without significant layout modifications.
The extensive use of nut spot welding machines can be attributed to their efficiency, cost-effectiveness, high welding strength, versatility, consistency, and space-saving design. These machines offer numerous advantages, including time savings, reduced labor costs, reliable weld quality, and the ability to weld a variety of materials. As a result, nut spot welding machines have become a preferred choice for many industries seeking efficient and reliable solutions for joining nuts to metal components.