This article explores the significance of using cooling water in butt welding machines. Cooling water plays a vital role in maintaining the equipment’s optimal performance and ensuring the integrity of welded joints. Understanding the reasons behind its usage is crucial for achieving efficient and high-quality welding operations.
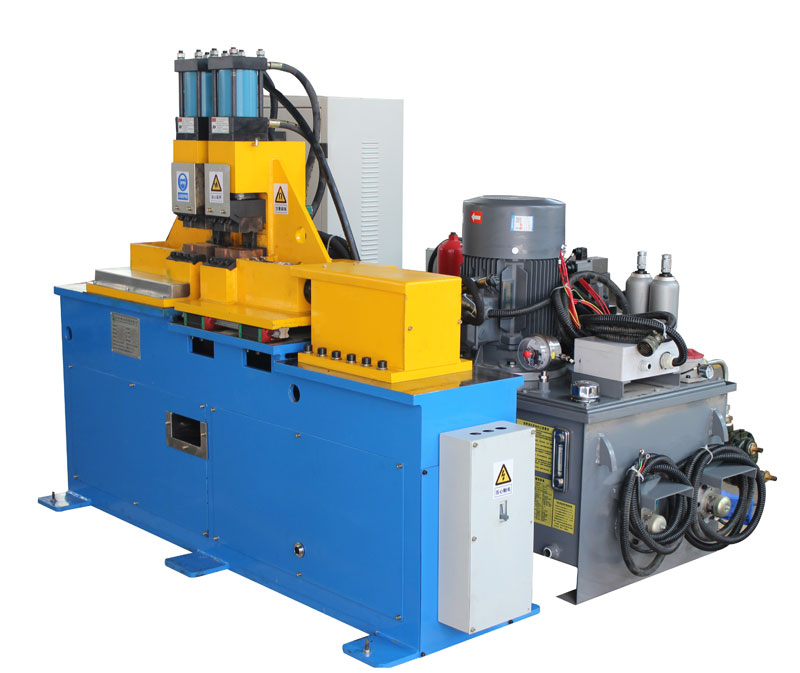
Introduction: Butt welding machines are commonly employed in industrial applications to achieve strong and reliable welded joints. These machines generate a considerable amount of heat during the welding process, which can impact their performance and the quality of the welds. Cooling water is employed to regulate the temperature and prevent overheating, ensuring the welding machine operates at its best capacity.
- Heat Dissipation: During welding, the intense heat generated at the welding electrode and the joint area can cause the equipment to overheat. Cooling water is circulated through the welding machine to absorb and dissipate this heat, preventing any damage to the components and maintaining stable operating temperatures.
- Protecting Components: Excessive heat can lead to the degradation of critical components in the welding machine, including the welding electrode, transformer, and other parts. Cooling water helps to safeguard these components from overheating, prolonging their lifespan and reducing the risk of breakdowns.
- Improving Weld Quality: Stable operating temperatures contribute to consistent weld quality. By keeping the welding machine cool, potential issues like metal distortion and thermal stress are minimized, resulting in stronger and more reliable welded joints.
- Increasing Efficiency: Cooling water maintains the welding machine’s efficiency by preventing unnecessary energy losses caused by overheating. This ensures smooth welding operations and reduces downtime, enhancing productivity in industrial settings.
- Safety Considerations: Using cooling water is essential for safety reasons. It helps prevent the welding machine from becoming too hot to handle, reducing the risk of burns or other accidents for operators and maintenance personnel.
In conclusion, cooling water is a critical element in the operation of butt welding machines. Its ability to dissipate heat, protect components, improve weld quality, increase efficiency, and enhance safety makes it an indispensable part of the welding process. By implementing proper cooling water systems, industries can ensure their butt welding machines perform optimally, delivering high-quality welded joints consistently and efficiently.