Bubbles or gas pockets in nut welding machine welds can significantly impact the quality and integrity of the joint. Understanding the causes of bubble formation is crucial for addressing and preventing this issue. This article explores the factors that contribute to bubble formation in nut welding machine welds and provides insights into effective mitigation strategies.
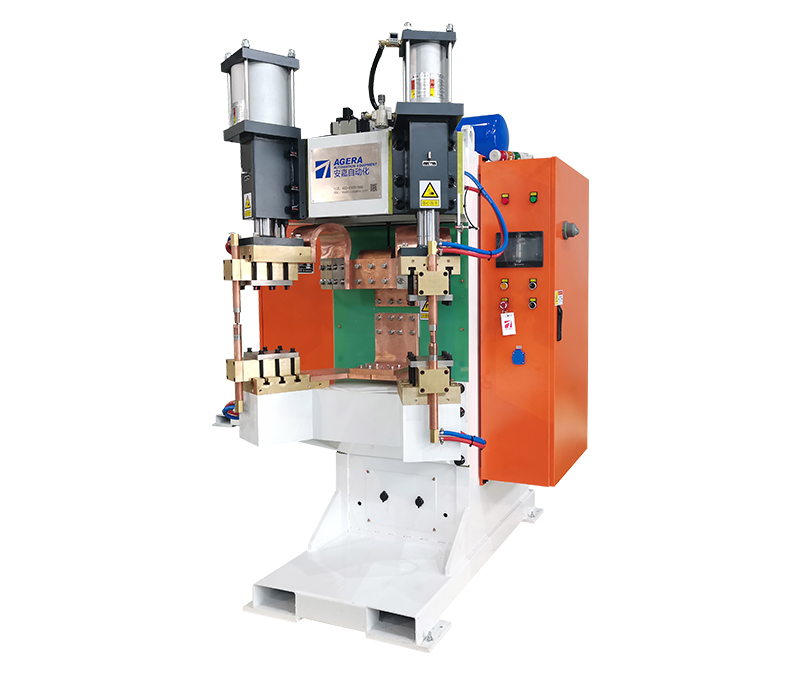
- Contamination:
- Contamination on the surface of the nut or welding material, such as oil, grease, or dirt, can trap air and create bubbles during the welding process.
- Thoroughly clean and degrease the nut and welding area prior to welding to minimize the presence of contaminants.
- Moisture:
- Moisture or humidity in the welding environment can vaporize and form gas bubbles during the welding process.
- Ensure proper moisture control in the welding area, including controlling humidity levels and keeping the welding materials dry.
- Improper Shielding Gas:
- Inadequate or improper shielding gas can lead to the formation of bubbles in the weld.
- Use the appropriate shielding gas based on the specific nut material and welding process, and ensure proper gas flow and coverage during welding.
- Incorrect Welding Parameters:
- Welding parameters such as current, voltage, and welding speed must be properly set to ensure the formation of sound welds.
- Improper parameter settings can create excessive heat and gas entrapment, leading to the formation of bubbles.
- Optimize welding parameters based on the nut material, thickness, and joint design to achieve consistent and defect-free welds.
- Welding Technique:
- Inconsistent or improper welding techniques, such as excessive or insufficient heat input, can contribute to bubble formation.
- Ensure proper arc control, travel speed, and electrode positioning during the welding process to minimize the likelihood of bubble formation.
- Material Compatibility:
- Incompatible materials or dissimilar metals can create metallurgical reactions that result in the formation of bubbles.
- Select compatible materials and ensure proper joint design to minimize the risk of metallurgical incompatibilities.
Bubbles in nut welding machine welds can compromise the structural integrity and quality of the joint. By addressing factors such as contamination, moisture, shielding gas, welding parameters, welding technique, and material compatibility, operators can significantly reduce or eliminate bubble formation. It is essential to follow proper cleaning procedures, control moisture levels, use appropriate shielding gas, optimize welding parameters, employ correct welding techniques, and select compatible materials. By implementing these measures, welders can achieve high-quality, bubble-free welds, ensuring the reliability and performance of nut joints.