Resistance spot welding machines are essential tools in various industries for joining metal components through the application of heat and pressure. However, there are certain situations and conditions where the use of these machines should be avoided to ensure safety, efficiency, and the longevity of equipment. In this article, we will explore the scenarios in which it is best to avoid using resistance spot welding machines.
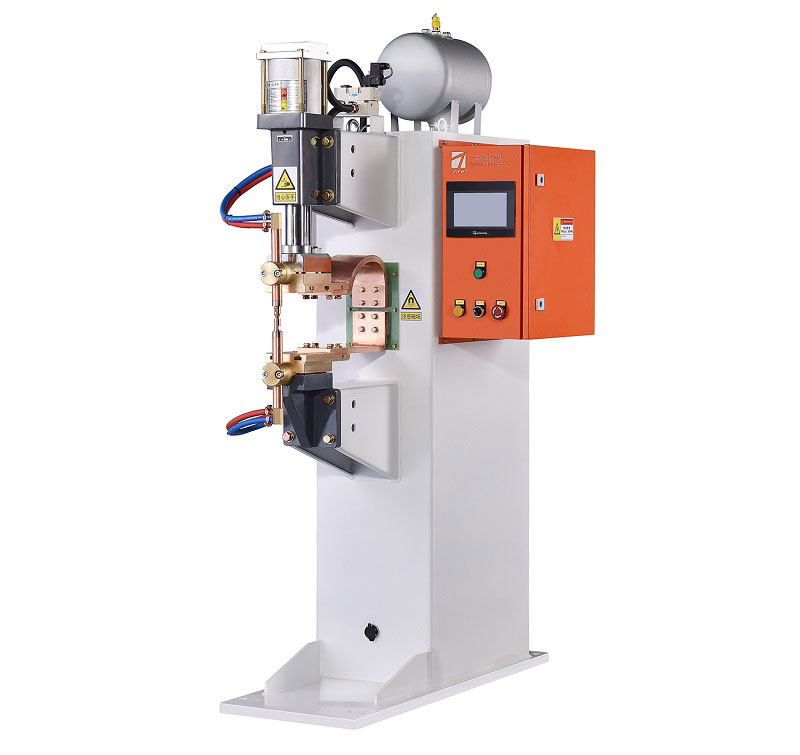
- Explosive Environments: One of the primary conditions to avoid using resistance spot welding machines is in explosive environments. These environments include places with flammable gases, vapors, or dust. The sparks generated during the welding process can serve as ignition sources, leading to catastrophic accidents.
- Poor Ventilation: In areas with inadequate ventilation, the fumes and gases produced during spot welding can accumulate, posing a health risk to the operators. The exposure to these harmful substances can cause respiratory problems and other health issues. Proper ventilation or the use of fume extraction systems is crucial in such environments.
- Inadequate Safety Measures: Resistance spot welding machines should never be operated without appropriate safety measures in place. This includes the use of personal protective equipment (PPE) such as welding helmets, gloves, and safety goggles. Ignoring safety precautions can result in serious injuries.
- Insufficient Training: Improper use of resistance spot welding machines due to lack of training can lead to poor weld quality, damage to equipment, and safety hazards. Operators should receive adequate training to operate these machines safely and effectively.
- Corrosive or Wet Environments: Exposure to corrosive substances or moisture can damage the welding equipment and compromise the quality of welds. It’s essential to keep the machines and workpieces dry and protected from corrosive materials.
- Overloading Equipment: Overloading a resistance spot welding machine beyond its specified capacity can lead to equipment failure, such as transformer burnout or electrode damage. It’s crucial to adhere to the machine’s rated capacity to prevent such issues.
- Inconsistent Material Thickness: When welding materials with significant variations in thickness, it’s advisable to avoid resistance spot welding. In such cases, alternative welding methods like MIG or TIG welding might be more suitable to ensure a strong and uniform bond.
- Highly Conductive Materials: Some highly conductive materials, like copper, can be challenging to weld using resistance spot welding due to their excellent heat dissipation properties. Specialized welding methods may be required for such materials.
- Remote or Inaccessible Locations: Resistance spot welding machines may not be suitable for welding in remote or hard-to-reach locations. In such cases, portable welding equipment or alternative joining techniques may be more practical.
In conclusion, resistance spot welding machines are valuable tools in various industries, but their use should be avoided in certain situations to ensure safety and efficiency. Proper training, adherence to safety protocols, and a clear understanding of the working environment are essential for the successful and safe use of these machines. Always prioritize safety and consider alternative welding methods when necessary to achieve the best results for your specific welding needs.