In the world of industrial manufacturing, welding is a fundamental process that plays a crucial role in joining components together. Nut spot welding is a specific method frequently employed in the assembly of various products, from automobiles to appliances. However, like any other welding process, it can encounter issues, two of which are particularly troublesome: weld spatter and de-welding. In this article, we will explore these problems and offer practical solutions to address them.
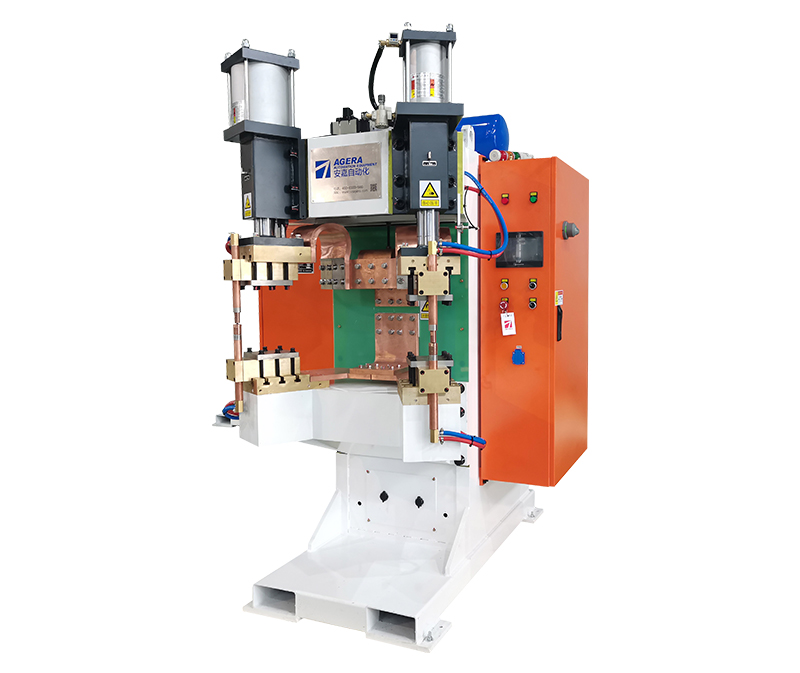
Weld Spatter: The Unwanted Residue
Weld spatter refers to the small, molten metal droplets that can splatter around the welding area during the nut spot welding process. These droplets often adhere to nearby surfaces, causing a range of issues, such as contamination, poor weld quality, and even safety concerns.
Causes of Weld Spatter
- Excessive Welding Current: One common cause of weld spatter is using too much welding current. This overheats the molten metal, making it more likely to splatter.
- Improper Electrode Size: Using the wrong electrode size can also lead to spatter, as it affects the heat distribution.
- Dirty or Contaminated Surfaces: Welding surfaces that are not properly cleaned can lead to spatter due to impurities on the material.
Solutions for Weld Spatter
- Adjust Welding Parameters: By reducing the welding current and ensuring the correct electrode size, you can minimize spatter.
- Proper Surface Preparation: Ensure that the surfaces to be welded are clean and free from contaminants.
- Anti-Spatter Sprays: Applying anti-spatter sprays or coatings to the workpiece and the welding gun nozzle can help reduce spatter.
De-welding: When Joints Break
De-welding, on the other hand, is the unintended separation of the welded nut from the base material. This problem can compromise the integrity of the final product and lead to costly rework or, in some cases, safety hazards.
Causes of De-welding
- Insufficient Weld Time: If the welding time is too short, the nut may not fuse properly with the base material.
- Inadequate Pressure: The pressure applied during the welding process is essential. Inadequate pressure can lead to incomplete welds.
- Material Mismatch: Using materials with vastly different melting points can result in de-welding due to unequal thermal expansion and contraction.
Solutions for De-welding
- Optimize Welding Parameters: Ensure that the welding time and pressure are set correctly for the specific materials being joined.
- Material Compatibility: Use materials with similar properties to minimize the risk of de-welding.
- Quality Control: Implement thorough quality control measures to detect and rectify de-welding issues early in the manufacturing process.
In conclusion, nut spot welding is a valuable technique in industrial manufacturing. However, weld spatter and de-welding are common challenges that can impede the welding process. By understanding their causes and implementing the suggested solutions, manufacturers can produce high-quality, reliable welds while minimizing production setbacks and costs. It’s essential to prioritize safety and quality when dealing with welding issues to ensure the long-term success of any manufacturing operation.