Spot welders are commonly used equipment in various industries, widely used to accurately and efficiently connect metal parts, in order to ensure its best performance and service life, regular inspection and maintenance of the equipment is important, this article will talk about what to pay attention to when conducting spot welder inspection.
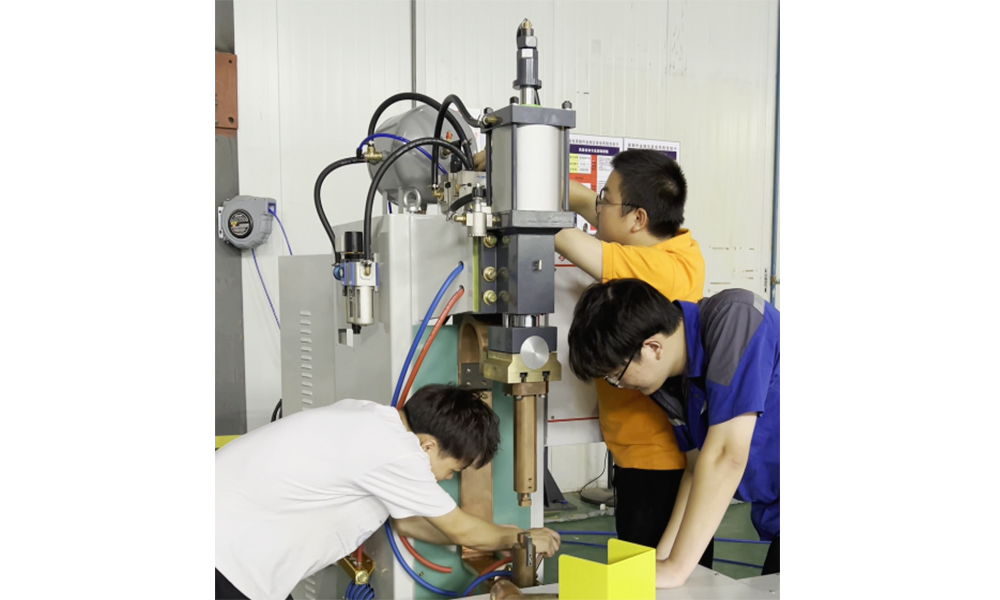
- Safety first: Before starting any inspection, it is necessary to ensure that the machine is disconnected from the power supply to prevent accidental start-up during the inspection. In addition, wear appropriate personal protective equipment (PPE), such as gloves and safety glasses. Protect yourself from potential hazards.
- External inspection: First visually inspect the external components of the welder, check the cables, connectors, electrodes and fixtures for obvious signs of wear or damage, and ensure that the heating system is working properly and the coolant circulation is free of defects.
- Electrode condition: Electrode condition has a significant impact on welding quality. Check whether the electrode has impact, deformation or pitting signs, if the electrode has wear phenomenon, it can be ground to maintain the consistency and reliability of the welding.
- Cable and connection inspection: Check welded cables and connections for signs of damage, exposure, or loose connections. Cable failure can cause arcing, which can be hazardous and affect weld quality.
- Power supply and control: Check the power supply and control panel for faults. Check that all buttons, switches, and knobs are working properly to ensure that they respond as expected.
- Cooling system: A cooling system is necessary to prevent overheating during long periods of operation. Check that the coolant level in the coolant reservoir is normal, and check that the coolant line is not clogged, and if necessary, you need to clean or replace it.
- Grounding and insulation: Proper grounding is very important for electrical safety and effective welding. Check the ground connection and ensure that cables and wires are strong and free of corrosion to prevent electrical short circuits.
- Weld quality: Weld tests are performed on the sample material to assess weld quality and consistency. If any irregularities are found, they may indicate a problem with the machine setup, electrodes, or other components.
- Maintenance: Check machine maintenance to ensure regular maintenance and calibration, which you should perform in a timely manner to avoid further complications.
- Professional inspections: Although regular visual inspections are valuable, it is recommended that equipment be inspected regularly by a qualified technician. A professional inspection can uncover problems that may not be detected during a visual inspection.Controlling the welder in an average position usually requires careful attention to all aspects, from safety measures to the condition of the electrodes, cables, controls and cooling systems. With comprehensive and customized controls, you can improve the performance and extend the life of the welder, minimize downtime and ensure safe operation. It is necessary in various industrial applications.
Controlling the welder in an average position usually requires careful attention to all aspects, from safety measures to the condition of the electrodes, cables, controls and cooling systems. With comprehensive and customized controls, you can improve the performance and extend the life of the welder, minimize downtime and ensure safe operation. It is necessary in various industrial applications.