Contact resistance is a critical concept in butt welding machines that directly affects the welding process’s efficiency and overall weld quality. Understanding the concept of contact resistance is essential for welders and professionals in the welding industry to optimize welding operations and achieve consistent and reliable weld results. This article explores contact resistance in butt welding machines, highlighting its significance and impact on the welding process.
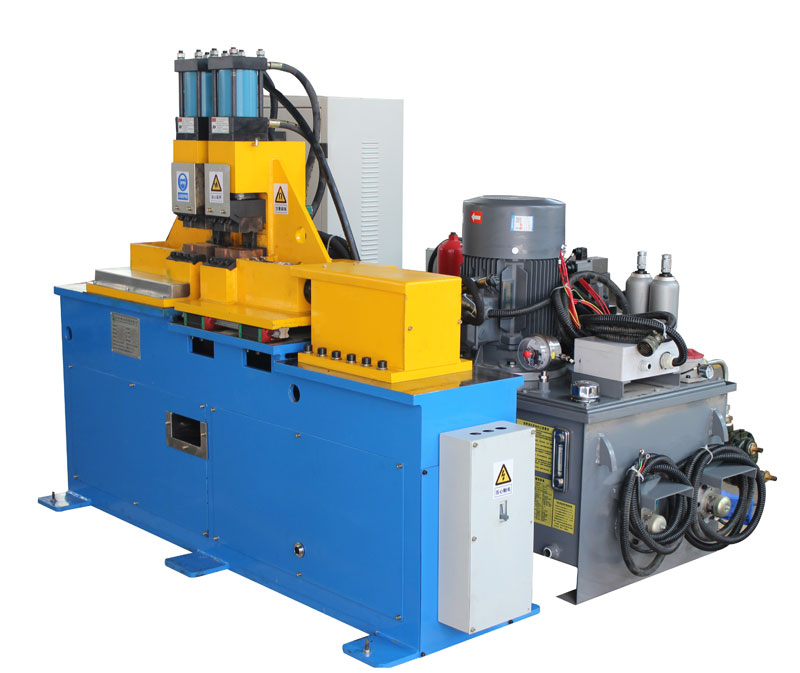
- Definition of Contact Resistance: Contact resistance refers to the electrical resistance that occurs at the interface between the welding electrode and the workpieces during welding. It is a crucial factor that influences the flow of welding current through the joint.
- Factors Affecting Contact Resistance: Several factors contribute to contact resistance, including the surface condition of the welding electrode and workpieces, the clamping force applied, and the cleanliness of the contact surfaces.
- Impact on Welding Efficiency: High contact resistance can impede the flow of welding current, leading to insufficient heat generation and poor fusion between the weld metal and the base metal. This, in turn, affects the welding efficiency and may result in incomplete penetration and weak welds.
- Measures to Reduce Contact Resistance: To minimize contact resistance, it is essential to ensure that the welding electrode and workpiece surfaces are clean and free from contaminants. Proper electrode alignment and adequate clamping force also help reduce contact resistance.
- Importance of Proper Contact Resistance: Achieving proper contact resistance is crucial for producing high-quality welds. It ensures that the welding current effectively flows through the joint, resulting in consistent and reliable weld bead formation.
- Monitoring and Control: Welding operators and professionals must monitor and control contact resistance during the welding process. Continual monitoring helps identify any fluctuations or deviations that may impact the weld quality.
- Impact on Welding Parameter Settings: Contact resistance can influence the selection of welding parameter settings, such as welding current and voltage. Proper adjustment of these parameters accounts for the resistance at the electrode-workpiece interface.
In conclusion, contact resistance is a significant factor in butt welding machines that directly affects welding efficiency and weld quality. Understanding the concept of contact resistance is essential for welders and professionals to optimize welding operations and achieve consistent and reliable weld results. By addressing factors that contribute to contact resistance and ensuring proper electrode alignment and clamping force, welding operators can minimize resistance and promote efficient welding. Monitoring and controlling contact resistance during the welding process play a crucial role in achieving high-quality welds with excellent fusion integrity and mechanical strength. Emphasizing the significance of contact resistance in butt welding machines fosters advancements in welding technology, supporting industries across diverse applications and sectors.