Resistance spot welding is a widely used joining technique in various industries, including automotive, aerospace, and electronics. Ensuring the quality of welds is crucial for product integrity and safety. In this article, we will discuss the key aspects that should be reflected in the quality of resistance spot welding.
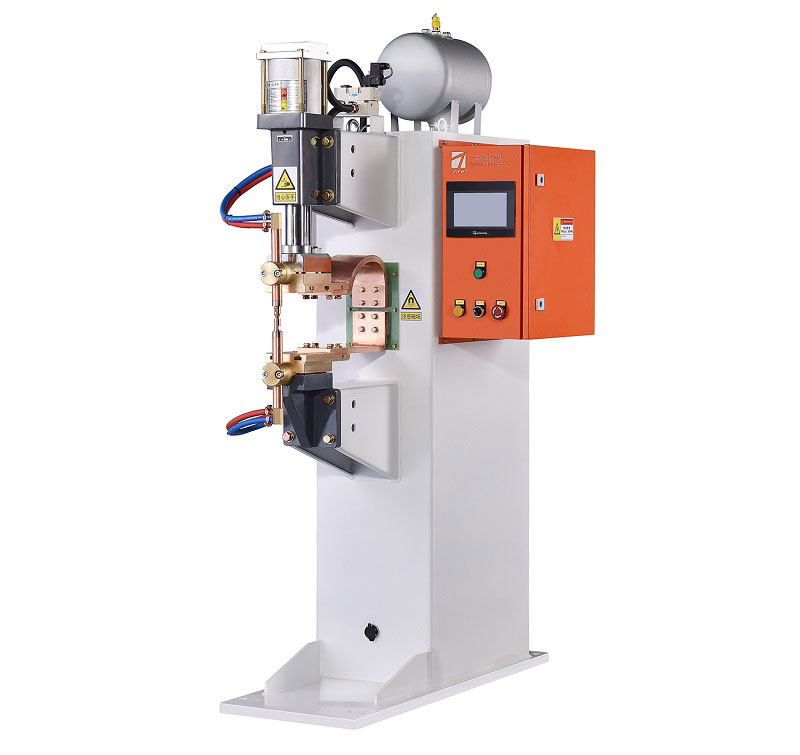
- Joint Strength: The primary objective of any welding process is to create a strong and durable joint. In resistance spot welding, the weld’s tensile and shear strength are of utmost importance. A high-quality weld should withstand the stresses and loads it will encounter during the product’s lifespan.
- Weld Appearance: The visual appearance of a weld can provide valuable insights into its quality. A well-executed resistance spot weld should exhibit a smooth and consistent surface, free from irregularities, cracks, or voids. Aesthetic considerations are particularly relevant in industries where appearance matters, such as automotive manufacturing.
- Weld Consistency: Consistency is key in manufacturing. Weld quality should not vary significantly from one weld to another. Consistent welds are essential for predictable performance and product reliability. Monitoring and maintaining process parameters are vital for achieving this consistency.
- Electrical Conductivity: Resistance spot welding relies on the flow of electrical current through the materials being joined. An important quality aspect is the electrical conductivity of the weld. Properly welded joints should have low electrical resistance to ensure efficient current flow.
- Heat Affected Zone (HAZ): The HAZ is the area surrounding the weld where the material’s properties may have been altered due to the welding process. Minimizing the size and impact of the HAZ is critical, especially when welding materials with specific thermal sensitivities.
- Weld Integrity Testing: Non-destructive testing methods, such as ultrasonic testing or X-ray inspection, can be employed to assess the internal integrity of resistance spot welds. These tests can identify hidden defects that may compromise the weld’s quality.
- Process Control: To consistently achieve high-quality resistance spot welds, meticulous process control is necessary. This involves monitoring and adjusting welding parameters, electrode condition, and material preparation. Proper training of operators is also essential.
- Corrosion Resistance: In industries where exposure to harsh environments is likely, the resistance of welds to corrosion is a significant quality consideration. Adequate material choice and post-weld treatments can enhance corrosion resistance.
- Regulatory Compliance: Depending on the industry, there may be specific regulations and standards governing the quality of resistance spot welds. Compliance with these standards is essential for product safety and legal requirements.
In conclusion, the quality of resistance spot welding should encompass a range of critical aspects, from the mechanical strength of the joint to its visual appearance and regulatory compliance. Achieving high-quality welds involves a combination of skillful workmanship, precise process control, and adherence to industry standards, all of which contribute to the overall performance and reliability of the welded components.