Nut spot welding machines, also known as stud welding machines, are versatile tools used in various industries for joining nuts to metal surfaces. These machines employ different control modes to ensure precise and reliable welds. In this article, we will explore the various control modes commonly used in nut spot welding machines.
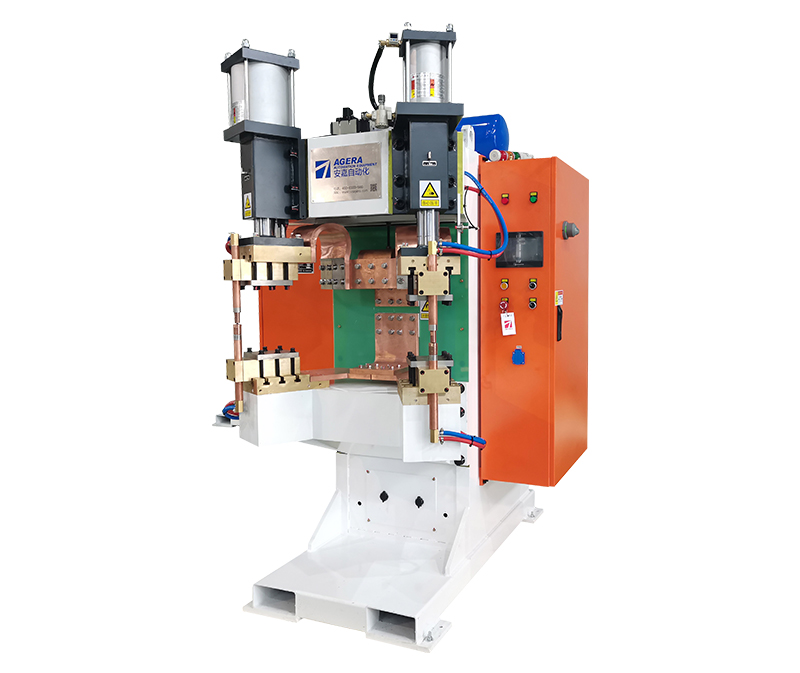
- Time-Based Control: One of the most basic control modes in nut spot welding machines is time-based control. In this mode, the operator sets the welding time, and the machine applies current to the nut and the workpiece for the specified duration. The weld quality depends on the operator’s ability to accurately set the time and the consistency of the applied pressure.
- Energy-Based Control: Energy-based control is a more advanced mode that considers both the welding time and the current level applied during that time. By controlling the energy input, this mode provides a more precise and consistent weld. It’s particularly useful when dealing with materials of varying thickness or when working with dissimilar metals.
- Distance-Based Control: In distance-based control, the machine measures the distance between the nut and the workpiece. This mode is commonly used for applications where the surface conditions or the thickness of the materials may vary. It ensures that the weld is initiated only when the nut is in close proximity to the workpiece.
- Force-Based Control: Force-based control relies on sensors to measure the force applied during the welding process. It ensures that a consistent force is maintained between the nut and the workpiece throughout the weld cycle. This control mode is beneficial when dealing with irregular or uneven surfaces.
- Pulse Control: Pulse control is a dynamic mode that uses a series of controlled pulses to create a weld. This mode is effective for reducing the risk of overheating and distortion in the workpiece, making it suitable for thin or heat-sensitive materials.
- Adaptive Control: Some modern nut spot welding machines are equipped with adaptive control systems. These systems use sensors and feedback mechanisms to monitor the welding process in real-time and make adjustments as needed. This ensures the highest quality welds under varying conditions.
- User-Programmable Control: User-programmable control modes allow operators to define custom welding parameters, including current, time, and any other relevant factors. This flexibility is valuable for applications that require specific welding conditions.
In conclusion, nut spot welding machines offer a range of control modes to cater to different welding requirements. The choice of control mode depends on factors such as the materials being joined, the application, and the desired weld quality. Understanding these control modes is crucial for achieving consistent and reliable welds in various industrial settings.