In recent years, the world of welding technology has witnessed a significant transformation with the emergence and evolution of capacitor energy storage spot welding machines. These cutting-edge welding devices have brought about a multitude of advantages, revolutionizing the welding industry. In this article, we will delve into the numerous benefits that these machines offer and how they have altered the landscape of modern welding.
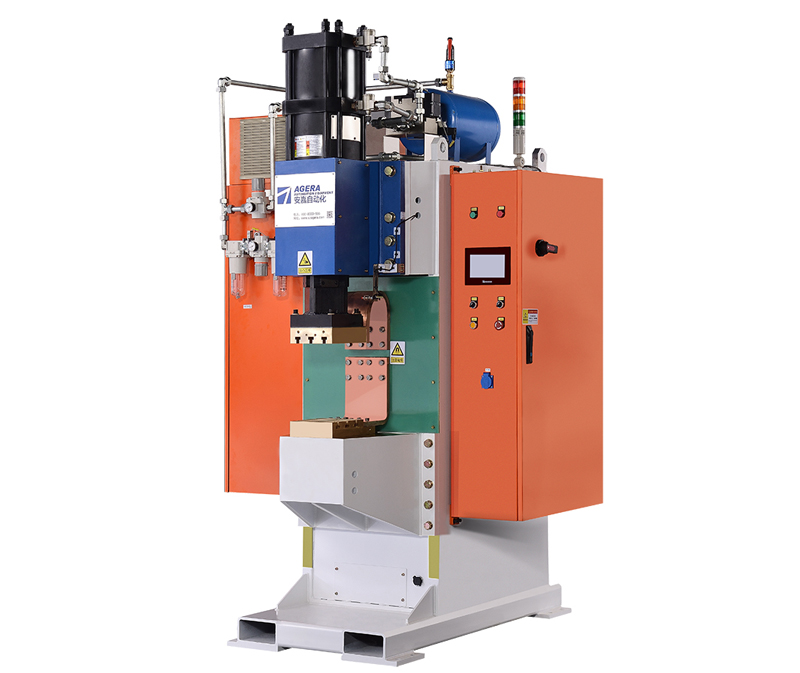
- Rapid Energy Release: Capacitor energy storage spot welding machines are designed to deliver high-intensity welding power in a matter of milliseconds. This rapid energy release allows for efficient and quick welding, significantly reducing the time needed for each welding operation. As a result, productivity in manufacturing has skyrocketed, making them invaluable in high-volume production settings.
- Minimal Heat Affected Zone (HAZ): Traditional welding methods often result in a substantial heat affected zone, which can weaken the structural integrity of the materials being joined. Capacitor energy storage spot welding, on the other hand, generates minimal heat during the welding process. This reduced heat input results in a smaller HAZ, preserving the material’s strength and integrity.
- Energy Efficiency: These machines are remarkably energy-efficient. By utilizing stored electrical energy, they minimize power consumption during welding cycles. This energy conservation not only reduces operational costs but also contributes to a greener, more sustainable welding process.
- Consistent Weld Quality: The precise control offered by capacitor energy storage spot welding machines ensures consistent weld quality. This uniformity is crucial in applications where structural integrity and safety are paramount, such as in the automotive and aerospace industries.
- Versatility: These machines can be employed in a wide range of welding applications, from thin sheets to thicker materials. Their adaptability makes them a valuable asset for various industries, from electronics to construction.
- Low Maintenance: Capacitor energy storage spot welding machines are known for their durability and low maintenance requirements. This reliability minimizes downtime, contributing to increased operational efficiency.
- Safety: Safety is a top priority in welding, and these machines excel in this aspect. Their design minimizes the risk of electrical shock and fire hazards, providing a secure working environment for welders.
- Reduction in Waste: Traditional welding methods often generate considerable waste in the form of slag and fumes. Capacitor energy storage spot welding is a clean process, producing minimal waste, which is particularly advantageous in industries aiming to reduce their environmental footprint.
- Economical: While the initial investment in these machines may be higher than traditional welding equipment, the long-term cost savings in terms of energy efficiency, reduced maintenance, and improved productivity make them a cost-effective choice for many businesses.
In conclusion, the development of capacitor energy storage spot welding machines has ushered in a new era in welding technology. Their advantages, including rapid energy release, minimal heat affected zone, energy efficiency, and versatility, have made them indispensable tools in various industries. As technology continues to evolve, it is likely that capacitor energy storage spot welding machines will become even more efficient and prevalent, further transforming the landscape of modern welding.