Nut projection welding is a widely used method for securely attaching nuts to metal components. However, occasional instances of loose welds can occur, compromising the strength and integrity of the joint. This article provides insights into the potential causes of loose welds in nut projection welding and offers practical solutions to address this issue, ensuring robust and reliable welds.
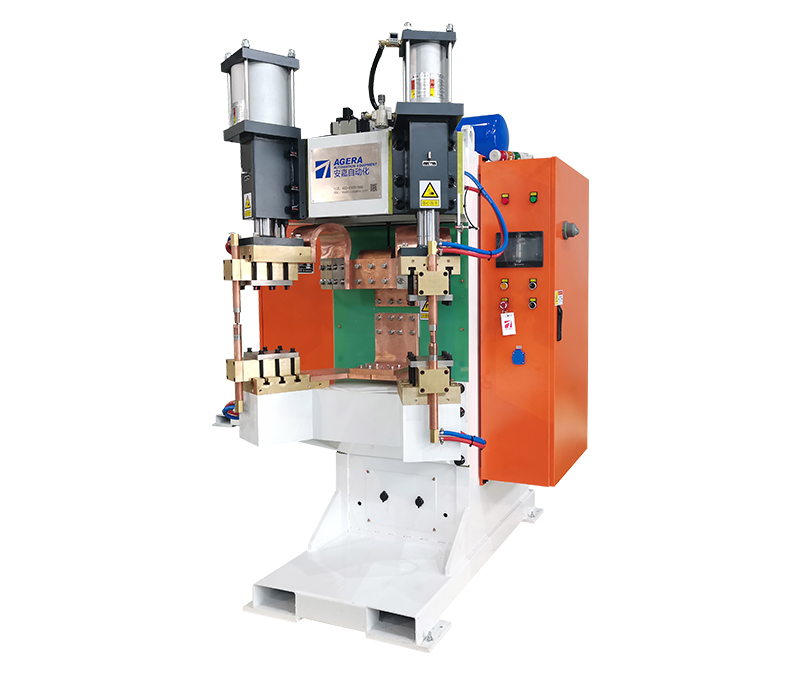
- Insufficient Welding Current: One possible cause of loose welds is an insufficient welding current. Inadequate current may result in insufficient heat generation, leading to weak weld formation. To address this, ensure that the welding machine is properly calibrated and delivering the appropriate current for the specific nut and workpiece combination. Adjusting the welding parameters to increase the current can help achieve stronger and more reliable welds.
- Improper Electrode Alignment: Incorrect alignment of the electrodes can also contribute to loose welds. If the electrodes are misaligned, the pressure applied during welding may not be evenly distributed, resulting in an inadequate bond between the nut and the workpiece. Verify that the electrodes are properly aligned and positioned to ensure optimal contact and pressure distribution. Regularly inspect and adjust the electrode alignment as necessary.
- Insufficient Welding Time: Insufficient welding time can lead to incomplete fusion and weak welds. The duration of the welding process should be sufficient to ensure proper heat transfer and complete melting of the nut and workpiece materials. Review the welding specifications and ensure that an appropriate welding time is set. Increase the welding time if necessary to achieve a more robust and reliable weld.
- Contamination or Oxidation: Contamination or oxidation on the surfaces being welded can hinder proper fusion and result in weak welds. Before welding, ensure that the nut and workpiece surfaces are clean and free from any contaminants, such as oil, dirt, or rust. Proper surface preparation, including cleaning and degreasing, is essential for promoting strong weld formation.
- Material Compatibility: Mismatched or incompatible materials can also contribute to weak welds. Ensure that the nut and workpiece materials are compatible and suitable for projection welding. Consider factors such as material composition, hardness, and thermal properties to ensure proper fusion and strong weld formation.
Addressing loose welds in nut projection welding requires a systematic approach to identify and rectify the underlying causes. By addressing potential issues related to welding current, electrode alignment, welding time, surface contamination, and material compatibility, manufacturers can enhance the quality and strength of welds in nut projection welding applications. Regular maintenance, proper calibration, and adherence to best practices can help ensure robust and reliable welds, strengthening the overall integrity of the joint.