Butt welding machines are widely used in various industries for joining metal components with speed and efficiency. To optimize production and achieve superior weld quality, adopting certain technical tips can significantly enhance the performance of spot welding machines. This article explores essential techniques that can boost productivity and improve the welding process for butt welding machines.
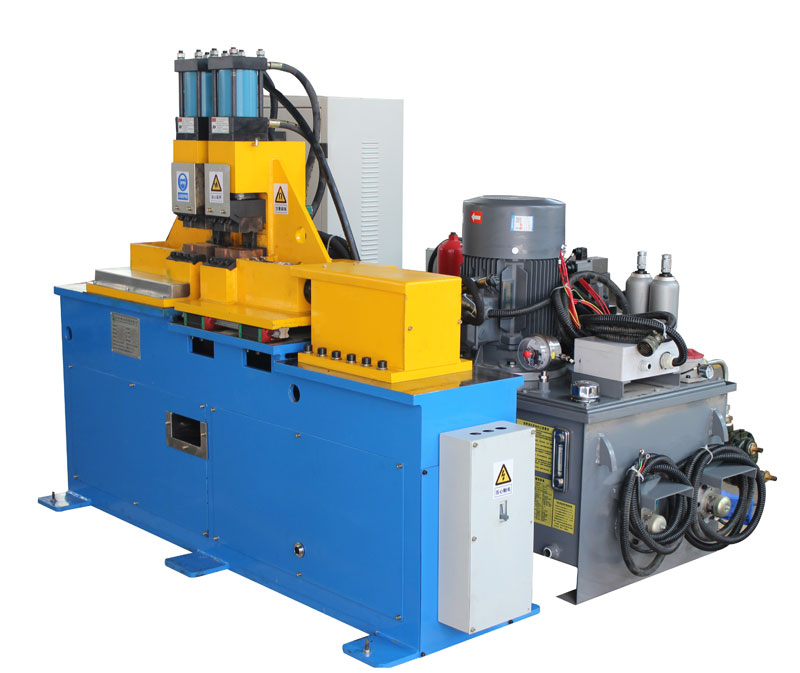
- Optimal Electrode Selection: Selecting the right electrodes is critical for achieving high-quality welds. Consider factors such as electrode material, shape, and size to ensure proper heat distribution and electrode life. Copper electrodes, for instance, are commonly used for their excellent conductivity and resistance to wear.
- Maintaining Electrode Cleanliness: Regularly cleaning electrodes is essential to prevent surface contamination and ensure consistent weld quality. Any residue or debris on the electrode can interfere with the welding process, leading to weaker welds. Implement a regular maintenance schedule to keep electrodes in prime condition.
- Accurate Welding Parameter Settings: Fine-tuning welding parameters such as welding current, time, and electrode force is essential for achieving optimal weld strength. Conducting test welds and evaluating the results can help determine the ideal parameter settings for specific material thicknesses and joint configurations.
- Monitoring Machine Performance: Implementing a robust monitoring system allows operators to track machine performance and detect any irregularities promptly. Real-time data on welding current, voltage, and force can help identify potential issues before they escalate, reducing downtime and production interruptions.
- Proper Electrode Alignment: Ensuring proper alignment of electrodes is crucial for uniform heat distribution during welding. Misaligned electrodes can result in uneven welds and compromise joint integrity. Regularly inspect and adjust electrode alignment to maintain consistent weld quality.
- Cooling System Efficiency: Efficient cooling systems are essential to prevent overheating of butt welding machines during prolonged operations. Proper cooling helps maintain the machine’s performance and extends the lifespan of critical components.
- Operator Training and Skill Enhancement: Investing in operator training and skill enhancement programs can significantly impact the overall performance of butt welding machines. Well-trained operators can troubleshoot issues, make informed decisions, and ensure proper machine operation for improved production outcomes.
Enhancing spot welding machine production techniques requires a combination of proper electrode selection, effective maintenance, accurate parameter settings, and efficient cooling systems. Additionally, operator training and monitoring machine performance are vital to achieving consistent and high-quality welds. By implementing these technical tips, manufacturers can elevate the performance of butt welding machines, increase productivity, and deliver reliable welded components to meet industry demands.