The efficiency of nut spot welding machines plays a crucial role in optimizing production processes and ensuring the timely delivery of high-quality products. Various factors can impact the performance and effectiveness of these machines. In this article, we will explore the three major factors that influence the efficiency of nut spot welding machines.
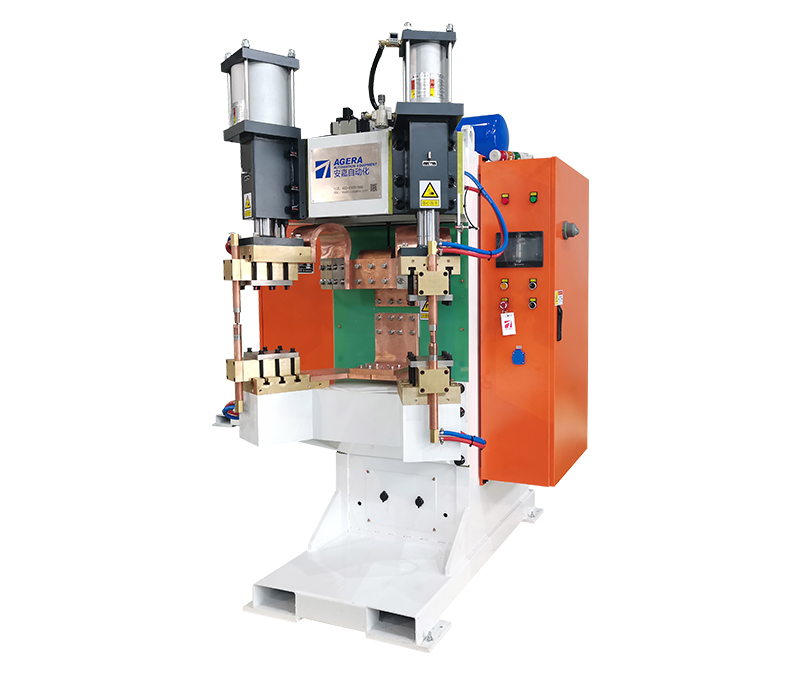
- Welding Process Parameters: The welding process parameters are among the primary factors that significantly affect the efficiency of nut spot welding machines. These parameters include welding current, welding time, electrode force, and electrode size. Properly setting and controlling these parameters are essential to achieving consistent and reliable welds. Inadequate or inaccurate parameter adjustments can lead to improper weld formation, increased cycle times, and reduced overall efficiency.
- Material and Design Compatibility: The choice of materials and design compatibility between the nut and the workpiece greatly impact the welding process efficiency. Using materials with dissimilar properties or inadequate joint designs can result in poor weld quality and reduced productivity. It is vital to select materials and joint designs that promote strong adhesion, even heat distribution, and efficient energy transfer during the welding process.
- Machine Maintenance and Calibration: Regular maintenance and calibration of the nut spot welding machine are critical to ensure its optimal performance. Wear and tear on electrodes, clamps, and other machine components can lead to inconsistencies in weld quality and increased downtime. Regular inspections, cleaning, and replacement of worn parts are necessary to maintain the machine’s efficiency and prolong its service life.
Conclusion: The efficiency of nut spot welding machines is influenced by several key factors, including welding process parameters, material and design compatibility, and machine maintenance and calibration. By carefully considering and optimizing these factors, manufacturers can enhance the performance of their nut spot welding machines, leading to increased productivity, improved weld quality, and cost-effective production processes. Investing in proper training, regular maintenance, and quality assurance measures can help ensure that nut spot welding machines operate at their peak efficiency, contributing to the overall success of manufacturing operations.