In the field of welding, the efficient dissipation of heat is crucial to ensure the optimal performance and longevity of welding equipment. One such essential cooling system used in nut welding machines is the water cooling system. This article explores the significance and functioning of the water cooling system in nut welding machines.
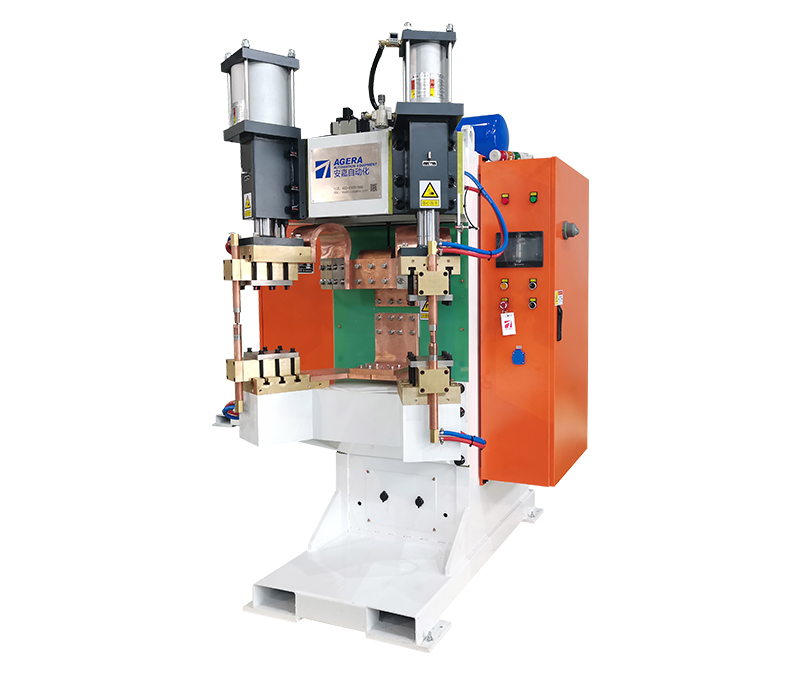
- Importance of Water Cooling: The nut welding process generates a considerable amount of heat, particularly during prolonged and high-intensity welding tasks. The water cooling system plays a vital role in preventing the welding machine from overheating by dissipating excess heat and maintaining stable operating temperatures.
- Components of the Water Cooling System: The water cooling system consists of various components, including a cooling pump, water reservoir, hoses, and a heat exchanger. The cooling pump circulates water throughout the system, while the heat exchanger facilitates the transfer of heat from the welding machine to the water.
- Cooling Process: During the welding process, heat is generated due to electrical resistance and energy transfer. The water cooling system works by passing coolant water through the heat exchanger, where it absorbs heat from the welding machine. The heated water then flows to the reservoir, where it cools down before being recirculated back to the heat exchanger.
- Advantages of Water Cooling: Water cooling offers several advantages over other cooling methods. It provides a continuous cooling effect, making it suitable for long welding sessions or high-duty cycles. The use of water cooling also reduces noise levels compared to air cooling systems. Additionally, the water cooling system is more energy-efficient, contributing to cost savings and reducing environmental impact.
- Maintenance and Precautions: Regular maintenance is essential to ensure the water cooling system’s proper functioning. Operators must inspect the cooling pump, hoses, and heat exchanger for leaks or damages regularly. The water level in the reservoir should be monitored, and the coolant water replaced periodically to maintain optimal cooling efficiency.
- Safety Considerations: Operators must exercise caution when handling the water cooling system to avoid electric shock or damage to the machine. Proper grounding and insulation of the system components are critical for safety. Additionally, the water cooling system should be positioned away from potential sources of water splashes or spills.
The water cooling system is a fundamental feature in nut welding machines, ensuring the stable operation and longevity of the equipment. By efficiently dissipating heat generated during the welding process, the water cooling system contributes to improved welding performance and increased productivity. Regular maintenance and adherence to safety guidelines are crucial in maximizing the benefits of this cooling system and enhancing the overall safety of the welding process.