Flash butt welding is a widely used technique in the manufacturing and construction industries for joining metals. It involves the use of high current and pressure to create a strong, durable bond between two metal pieces. One critical aspect of the flash butt welding process is preheating, which plays a significant role in achieving successful welds. In this article, we will explore the importance of preheating and its effects on the quality and integrity of flash butt welds.
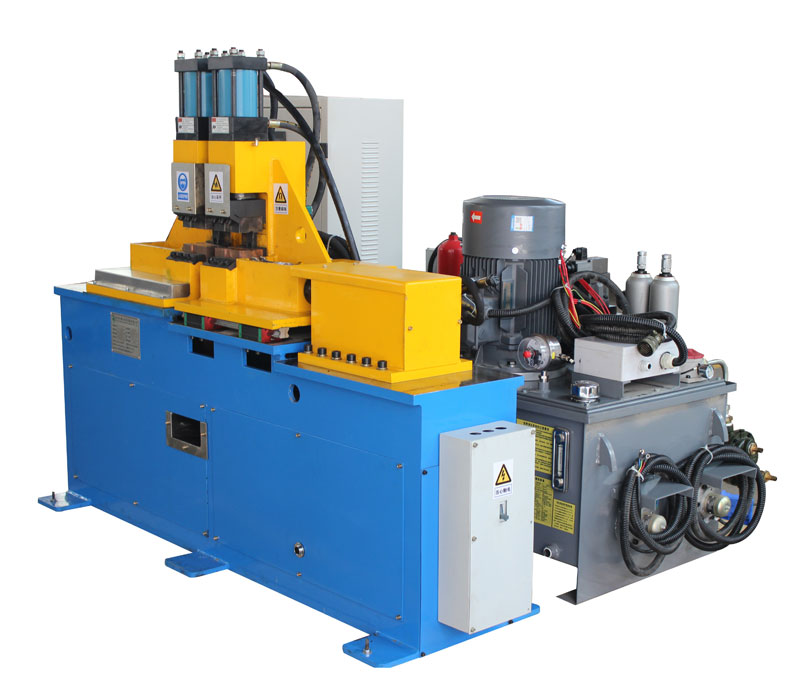
Preheating is the process of raising the temperature of the materials to be welded before the actual welding operation. It is typically done using induction heating, gas flames, or resistance heating methods. The primary objective of preheating in flash butt welding is to minimize the thermal stresses and temperature differentials that can occur during the welding process.
- Stress Reduction: Preheating helps reduce the internal stresses in the materials being welded. When metals are rapidly heated during welding, they expand, and as they cool down, they contract. This rapid expansion and contraction can result in residual stresses within the welded joint. Preheating allows for a more gradual temperature change, minimizing the risk of cracking and distortion in the welded pieces.
- Improved Material Flow: During flash butt welding, the materials are subjected to intense pressure and current, causing them to become highly malleable. Preheating softens the materials, making them more ductile and promoting better material flow. This improved material flow ensures that the metals fuse together smoothly, creating a strong and reliable bond.
- Reduced Hardening and Brittleness: Rapid cooling after welding can lead to the formation of hard and brittle microstructures in the welded joint. Preheating slows down the cooling process, allowing for the formation of softer and more ductile microstructures. This, in turn, enhances the overall toughness and ductility of the weld, reducing the risk of cracking and failure.
- Corrosion Resistance: Preheating can also have a positive impact on the corrosion resistance of the welded joint. By promoting the formation of a more uniform and less brittle weld, preheating helps reduce the susceptibility of the joint to corrosion and other forms of material degradation.
In conclusion, preheating is a crucial step in flash butt welding, as it contributes to the overall quality and integrity of the weld. By reducing internal stresses, improving material flow, minimizing hardening and brittleness, and enhancing corrosion resistance, preheating ensures that the welded joint meets the required performance and durability standards. Welders and manufacturers should carefully consider preheating parameters to achieve successful flash butt welds in various applications.