The power rectification component plays a critical role in energy storage spot welding machines by converting alternating current (AC) power from the mains supply into direct current (DC) power suitable for charging the energy storage system. This article provides an overview of the function and importance of the power rectification section in energy storage spot welding machines, highlighting its role in ensuring efficient and reliable operation.
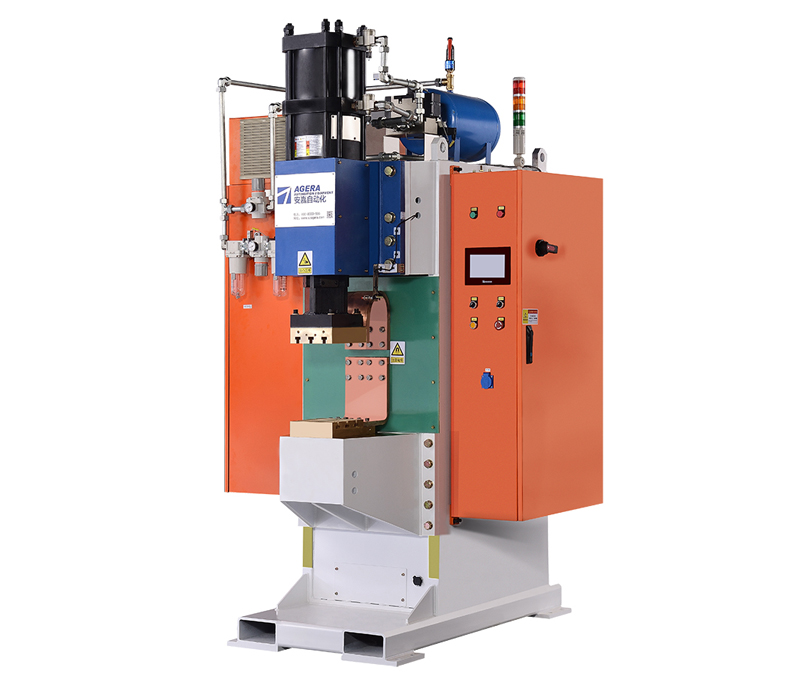
- Power Conversion: The power rectification section is responsible for converting AC power into DC power. It uses rectifier circuits, such as diodes or thyristors, to rectify the incoming AC voltage waveform, resulting in a pulsating DC waveform. This conversion is essential because the energy storage system typically requires DC power for charging and discharging operations.
- Voltage Regulation: In addition to converting AC to DC power, the power rectification section also performs voltage regulation. It ensures that the rectified DC output voltage remains within the desired range to meet the requirements of the energy storage system. Voltage regulation is achieved through control mechanisms, such as feedback circuits and voltage regulators, which monitor and adjust the output voltage accordingly.
- Filtering and Smoothing: The rectified DC waveform produced by the power rectification section contains undesirable ripple or fluctuations. To eliminate these fluctuations and obtain a smooth DC output, filtering and smoothing components are employed. Capacitors and inductors are commonly used to filter out high-frequency components and reduce voltage ripples, resulting in a stable and continuous DC power supply.
- Power Factor Correction (PFC): Efficient power utilization is a crucial aspect of energy storage spot welding machines. The power rectification section often includes power factor correction techniques to improve power efficiency and reduce energy wastage. PFC circuits actively correct the power factor by adjusting the input current waveform, aligning it with the voltage waveform, and reducing reactive power consumption.
- System Reliability and Safety: The power rectification section incorporates safety features and protection mechanisms to ensure the reliable and safe operation of the welding machine. Overvoltage protection, overcurrent protection, and short-circuit protection are implemented to safeguard the rectification components and prevent damage to the system. These safety measures contribute to the overall reliability and longevity of the equipment.
The power rectification section plays a crucial role in energy storage spot welding machines by converting AC power into regulated and filtered DC power for charging the energy storage system. By performing power conversion, voltage regulation, filtering, and smoothing, as well as incorporating power factor correction and safety features, this section ensures efficient and reliable operation of the welding machine. Manufacturers continue to advance power rectification technology to enhance energy efficiency, improve power quality, and maintain the highest level of safety in energy storage spot welding applications.