Forging pressure is a critical parameter in nut spot welding, as it directly influences the quality and strength of the weld joint. This article provides an overview of the effects of forging pressure on nut spot welds, highlighting its significance and its impact on weld integrity and mechanical properties.
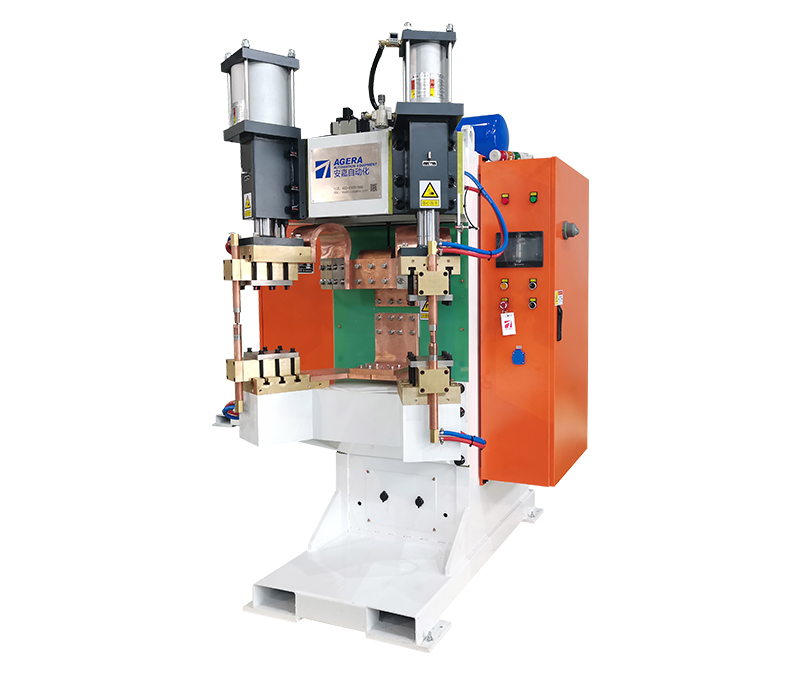
- Importance of Forging Pressure: Forging pressure plays a vital role in nut spot welding by exerting a compressive force on the workpieces during the welding process. This pressure ensures intimate contact between the nut and the base material, promoting material flow and enhancing the formation of a strong and durable weld. It helps in reducing air gaps, eliminating voids, and enhancing the metallurgical bond between the two components.
- Effects of Forging Pressure on Weld Integrity: a. Improved Contact: The application of forging pressure helps to establish and maintain proper contact between the nut and the base material. This intimate contact ensures efficient heat transfer and promotes the diffusion of atoms across the interface, leading to a robust and metallurgically bonded joint. b. Reduced Resistance: The compressive force exerted by forging pressure reduces the electrical resistance at the contact interface, facilitating the passage of current and enabling effective joule heating for fusion. c. Enhanced Material Flow: The application of forging pressure promotes material flow and redistribution, resulting in the expulsion of contaminants and the elimination of surface irregularities. This enhances the overall quality and integrity of the weld. d. Reduction of Porosity: Adequate forging pressure helps to eliminate porosity within the weld zone by compressing and displacing any trapped gases or impurities. This leads to a more consistent and defect-free weld structure. e. Increased Weld Strength: The proper application of forging pressure ensures optimal material compaction and intermolecular bonding, resulting in welds with improved mechanical properties, such as higher tensile strength and fatigue resistance.
- Optimal Forging Pressure: The appropriate forging pressure in nut spot welding depends on various factors, including the material properties, joint configuration, and desired weld characteristics. It is crucial to balance the applied pressure to achieve adequate material flow and bonding without causing excessive deformation or material damage.
Forging pressure plays a crucial role in nut spot welding, influencing the quality and strength of the weld joint. By promoting intimate contact, enhancing material flow, and reducing defects, the proper application of forging pressure ensures robust and reliable welds. Understanding the effects of forging pressure helps operators optimize the welding process, leading to superior weld integrity and mechanical properties.