Fixtures, also known as clamps or jigs, play a crucial role in butt welding machines, enabling precise and secure positioning of workpieces during welding operations. Understanding the significance of fixtures is essential for welders and professionals in the welding industry to achieve accurate fit-up and consistent weld results. This article explores the role of fixtures in butt welding machines, highlighting their functionalities and importance in ensuring successful welding processes.
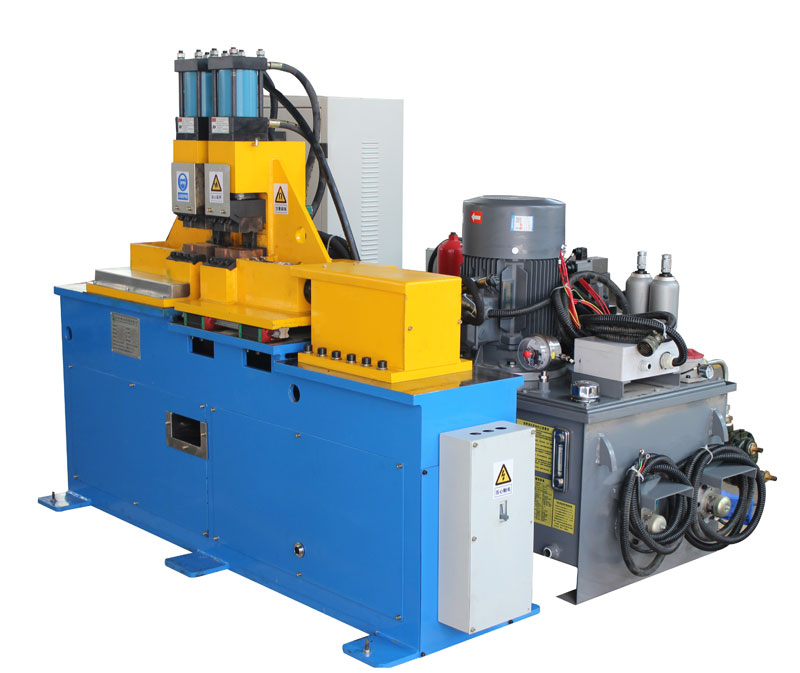
The Role of Fixtures in Butt Welding Machines:
- Accurate Fit-Up: Fixtures in butt welding machines are designed to hold and align workpieces with precision. Their primary role is to ensure accurate fit-up of the joint, promoting uniform contact between the welding electrode and the workpiece surfaces.
- Secure Clamping: Fixtures provide a secure clamping mechanism to hold the workpieces firmly in place during welding. This ensures that the joint remains stable and immobile throughout the welding process, preventing misalignment and distortion.
- Repeatable Welding Positions: By using fixtures, welders can achieve repeatable welding positions for consistent weld results. Fixtures maintain the workpieces’ orientation, allowing welders to reproduce the same weld parameters and electrode movement for multiple welds.
- Versatility and Adaptability: Fixtures can be designed for various joint configurations, making them adaptable to different welding requirements. Welders can use interchangeable fixtures to accommodate diverse workpiece sizes and shapes.
- Enhanced Safety: Using fixtures enhances safety during welding operations. The secure clamping and stable positioning reduce the risk of accidents caused by workpiece movement or unexpected shifts during welding.
- Time Efficiency: Fixtures contribute to time efficiency in butt welding processes. Once the workpieces are clamped in place, welders can focus on the welding parameters and electrode movement without worrying about constant readjustment.
- Automation Integration: Fixtures facilitate automation integration in butt welding machines. Automated systems can easily manipulate the fixtures for repetitive welding tasks, streamlining production processes and improving productivity.
In conclusion, fixtures play a fundamental role in butt welding machines, providing accurate fit-up, secure clamping, repeatable welding positions, versatility, safety, time efficiency, and compatibility with automation systems. Their functionalities are critical in achieving precise and reliable welding results, ensuring uniform weld quality and consistent joint alignment. Understanding the significance of fixtures empowers welders and professionals to optimize welding processes and meet industry standards. Emphasizing the importance of these essential components supports advancements in welding technology, promoting excellence in metal joining across diverse industrial applications.