Excessive welding current in resistance spot welding machines can lead to a range of problems, including weld defects, equipment damage, and safety hazards. In this article, we will explore the causes and consequences of this issue and discuss potential solutions.
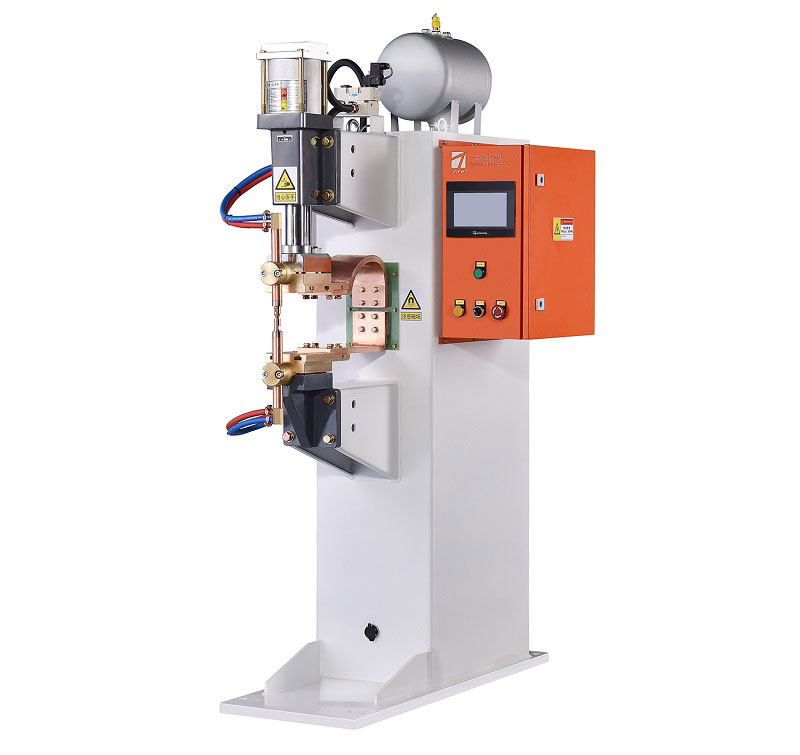
Resistance spot welding is a widely used process in manufacturing, especially in the automotive and aerospace industries. It involves the use of an electric current to create a weld between two metal sheets by generating heat at the point of contact. Controlling the welding current is crucial for achieving high-quality welds and ensuring the longevity of the welding equipment.
The causes of excessive welding current can vary, but some common factors include:
- Material Variations: Differences in the thickness or composition of the materials being welded can affect the resistance and, consequently, the required welding current.
- Electrode Wear: Over time, the electrodes used in spot welding machines can degrade, increasing resistance and necessitating higher welding currents to maintain proper weld quality.
- Poor Electrode Alignment: Misalignment of the electrodes can lead to uneven contact between the materials, resulting in increased resistance and the need for higher currents.
The consequences of excessive welding current are significant:
- Weld Defects: High current can cause overheating and excessive melting, leading to weld spatter, cracks, or even burn-through, compromising the integrity of the weld.
- Equipment Damage: Prolonged use of excessive current can damage electrodes, transformers, and other components of the spot welding machine, leading to costly repairs or replacements.
- Safety Hazards: High welding currents increase the risk of electrical arcing, which can pose serious safety hazards to operators and equipment.
To address this issue, manufacturers and operators can take several steps:
- Regular Maintenance: Implement a maintenance schedule to regularly inspect and replace worn electrodes and ensure proper alignment of the welding machine.
- Process Monitoring: Use monitoring systems that can detect variations in welding current and provide real-time feedback to operators, allowing them to make immediate adjustments.
- Material Testing: Test materials to determine the appropriate welding current settings for each job, taking into account material thickness and composition.
- Training: Ensure that operators are trained in the proper use of the welding equipment and understand how to adjust current settings based on the specific welding task.
In conclusion, excessive welding current in resistance spot welding machines can lead to a host of issues, but with proper maintenance, monitoring, and training, these problems can be mitigated. Controlling welding current is essential for achieving high-quality welds, extending the life of equipment, and ensuring the safety of operators and the workplace.