Voltage and current are two critical parameters that significantly influence the welding process in energy storage spot welding machines. The selection and control of these parameters play a vital role in achieving desired weld quality, strength, and overall performance. This article aims to explore the effects of voltage and current on welding in energy storage spot welding machines, highlighting their importance and providing insights into optimizing these parameters for successful welds.
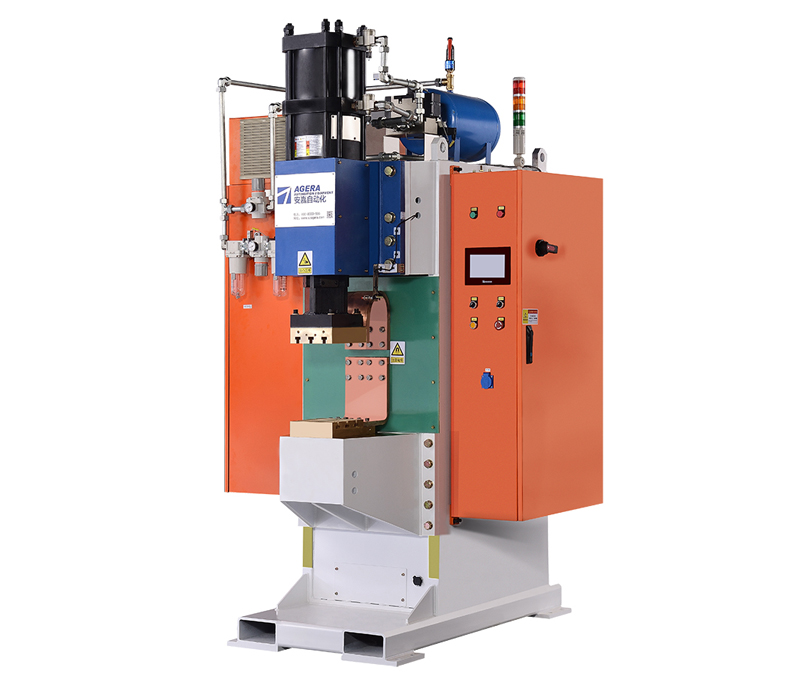
- Voltage: Voltage is a key factor that affects the heat generation and penetration during welding. The voltage level determines the intensity of the electrical discharge between the electrodes, which ultimately affects the weld pool formation and fusion of the workpiece. Higher voltages result in increased heat input, deeper penetration, and larger weld nugget size. Conversely, lower voltages produce shallower penetration and smaller weld nuggets. It is essential to select the appropriate voltage based on the material thickness, joint design, and desired weld characteristics.
- Current: Current is another crucial parameter that influences the welding process. It determines the amount of heat generated during the electrical discharge, affecting the melt pool size, weld penetration, and overall energy input. Higher currents result in greater heat input, leading to larger weld nuggets and improved fusion. However, excessively high currents can cause spattering, electrode sticking, and potential damage to the workpiece. Lower currents may result in inadequate fusion and weak welds. Optimal current selection depends on factors such as material properties, joint configuration, and welding speed.
- Voltage-Current Relationship: The relationship between voltage and current is interdependent and should be carefully balanced for successful welding. Increasing the voltage while keeping the current constant leads to higher heat input and deeper penetration. Conversely, increasing the current while maintaining a constant voltage level increases heat input and the width of the weld nugget. It is crucial to find the optimal combination of voltage and current that achieves the desired weld characteristics without compromising the integrity of the workpiece.
- Weld Quality Considerations: Proper control of voltage and current is essential for achieving consistent and high-quality welds. Insufficient voltage or current may result in incomplete fusion, weak joints, or insufficient penetration. Excessive voltage or current can cause excessive heat input, leading to distortion, spatter, or even material damage. Operators should carefully evaluate the material properties, joint design, and welding requirements to determine the appropriate voltage and current settings for each application.
Voltage and current are critical parameters in energy storage spot welding machines that significantly impact the welding process. Finding the right balance between these parameters is essential for achieving optimal weld quality, strength, and integrity. Operators should consider the material properties, joint configuration, and desired weld characteristics when selecting and adjusting voltage and current levels. Proper control of these parameters ensures consistent and reliable welds, leading to improved productivity and overall welding performance in energy storage spot welding machines.