The potential difference, also known as the voltage, plays a crucial role in the welding process of nut welding machines. Understanding the influence of potential difference on welding is essential for achieving optimal weld quality. This article explores the effects of potential difference on welding in nut welding machines and provides insights into its significance in the welding process.
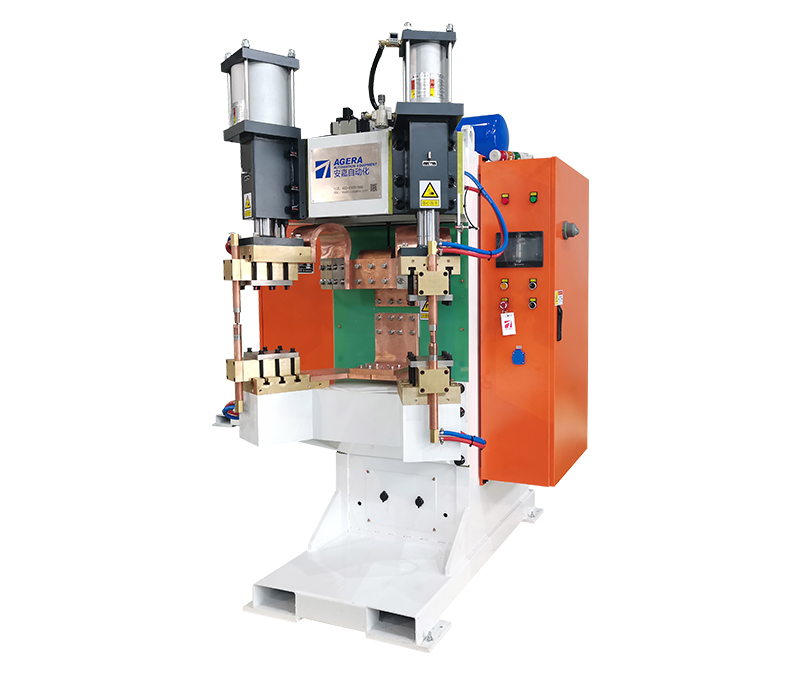
- Heat Generation:
- The potential difference determines the heat generated during welding.
- Higher voltages result in increased heat input, which affects the weld pool size, penetration depth, and overall energy transfer.
- Lower voltages may lead to insufficient heat input, resulting in inadequate fusion and weaker welds.
- Arc Stability:
- The potential difference affects the stability and characteristics of the welding arc.
- Proper voltage selection ensures a stable and well-defined arc, promoting consistent and controlled heat distribution.
- Inadequate voltage can cause arc instability, resulting in spatter, erratic weld bead formation, and potential defects.
- Metal Transfer:
- The potential difference influences the mode of metal transfer during welding.
- Higher voltages facilitate a more pronounced spray transfer mode, suitable for higher deposition rates and deep penetration.
- Lower voltages promote a globular or short-circuiting transfer mode, suitable for lower heat input and thinner materials.
- Electrode Life:
- The potential difference affects the wear and consumption rate of the welding electrode.
- Higher voltages can increase electrode erosion and result in shorter electrode life.
- Lower voltages generally lead to longer electrode life but may require additional passes to achieve desired weld dimensions.
- Electrical Efficiency:
- The potential difference impacts the electrical efficiency of the welding process.
- Selecting an appropriate voltage level ensures optimal power utilization and energy efficiency.
- Higher voltages may consume more electrical power, while lower voltages may reduce the overall welding speed.
The potential difference is a critical parameter in the welding process of nut welding machines. It influences heat generation, arc stability, metal transfer, electrode life, and electrical efficiency. Selecting the appropriate voltage level is crucial for achieving desired weld characteristics, such as penetration, fusion, and overall weld quality. Welding operators should consider the specific application, material thickness, joint design, and desired welding parameters to determine the optimal potential difference for each welding operation. By understanding and controlling the potential difference, welders can achieve high-quality welds with improved efficiency and performance in nut welding applications.