Flash butt welding is a widely used process in the manufacturing and construction industries. It involves the joining of two metal pieces by generating a high-intensity flash that melts the ends of the workpieces, followed by forging them together to form a solid weld joint. The flash-to-heat curve, a critical parameter in this process, plays a significant role in determining the quality of the weld and the efficiency of the welding machine. In this article, we will explore the influence of the flash-to-heat curve on the heating process and its implications for flash butt welding.
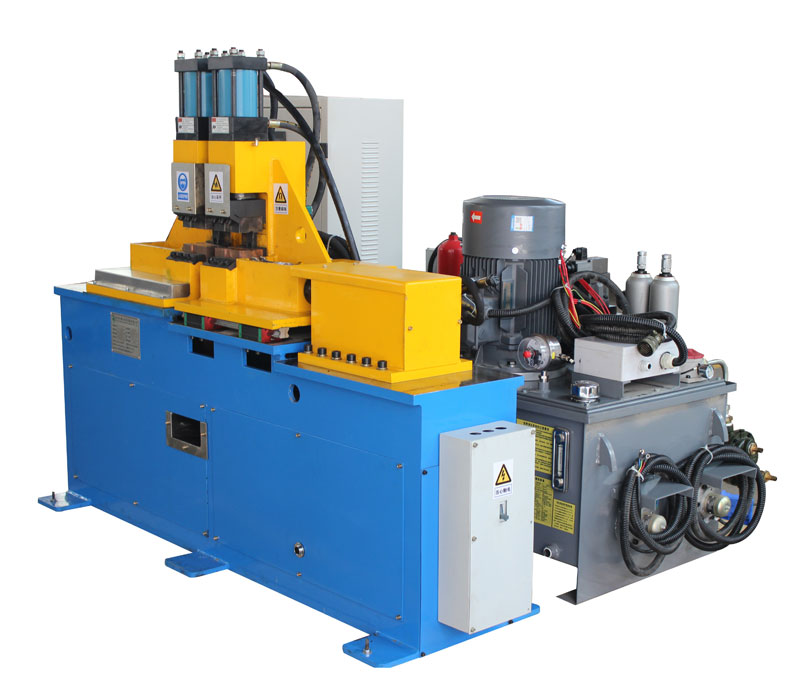
- Understanding the Flash-to-Heat Curve The flash-to-heat curve represents the relationship between the duration of the flashing phase and the amount of heat generated during the welding process. It is a fundamental factor in flash butt welding as it directly affects the quality of the weld and the energy consumption of the machine. The curve is typically characterized by three main phases: ignition, flashing, and forging.
- Impact on Heating The shape and characteristics of the flash-to-heat curve have a significant influence on the heating process during flash butt welding. A well-designed curve ensures that the flash duration and energy input are precisely controlled, leading to uniform heating of the workpieces. This uniform heating is essential to avoid defects such as cracking and distortion in the weld joint.
- Efficiency and Energy Consumption The flash-to-heat curve also plays a crucial role in determining the efficiency of the welding machine. An optimized curve can reduce energy consumption by minimizing the duration of the flashing phase while maintaining the required heat input. This not only reduces operational costs but also makes the welding process more environmentally friendly.
- Weld Quality The quality of the weld joint is directly linked to the flash-to-heat curve. A curve that allows for precise control of the flashing and forging phases ensures a strong and reliable weld. Variations in the curve can lead to issues like incomplete fusion, porosity, or excessive heat-affected zones, which can compromise the integrity of the weld.
- In summary, the flash-to-heat curve is a critical parameter in flash butt welding machines. Its influence on the heating process, energy consumption, and weld quality cannot be understated. Engineers and operators must carefully design and monitor this curve to achieve optimal welding results. Understanding and controlling the flash-to-heat curve is essential for ensuring the efficiency and reliability of flash butt welding in various industrial applications.