Resistance spot welding is a widely used process in manufacturing, particularly in the automotive and aerospace industries. It involves the joining of two metal sheets by passing a high electrical current through them at a specific location. One critical factor that can affect the quality and efficiency of resistance spot welding is contact resistance. In this article, we will explore the influence of contact resistance on the performance of resistance spot welding machines.
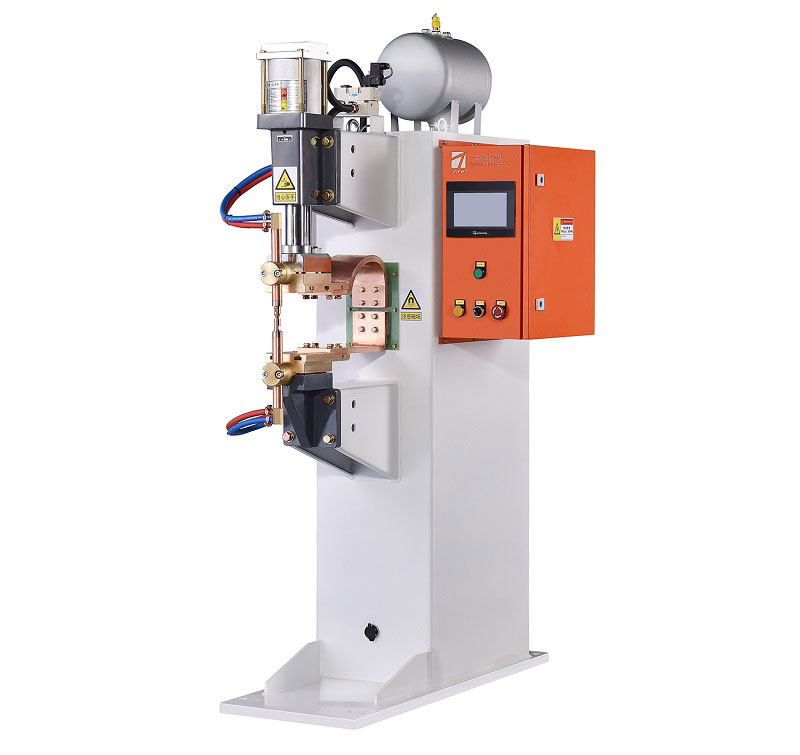
Understanding Contact Resistance:
Contact resistance refers to the opposition to the flow of electrical current at the interface between the welding electrodes and the workpieces being welded. It occurs due to the imperfections and surface conditions of the materials in contact. This resistance can result in several significant effects during the welding process.
Effects of Contact Resistance:
- Heat Generation: Contact resistance leads to the generation of heat at the electrode-workpiece interface. This additional heat can affect the temperature distribution in the weld zone, potentially causing inconsistencies in the weld nugget’s size and strength.
- Energy Loss: High contact resistance can result in energy loss in the welding process. A significant portion of the electrical energy may dissipate as heat at the contact points instead of being used for welding, making the process less efficient.
- Electrode Wear: Excessive contact resistance can accelerate electrode wear. As the electrodes degrade, the quality and consistency of the welds produced by the machine may deteriorate over time, leading to increased maintenance and operational costs.
- Weld Quality: Variations in contact resistance can lead to inconsistent weld quality. Inconsistent welds can compromise the structural integrity of the final product, posing safety and reliability concerns, especially in critical applications like automotive manufacturing.
Minimizing the Impact of Contact Resistance:
To mitigate the negative effects of contact resistance in resistance spot welding machines, several strategies can be employed:
- Electrode Maintenance: Regular maintenance and cleaning of the welding electrodes can help reduce contact resistance and prolong electrode life.
- Optimized Parameters: Adjusting welding parameters, such as current, time, and pressure, can help compensate for the effects of contact resistance and produce consistent welds.
- Improved Material Preparation: Ensuring that the surfaces to be welded are clean and free from contaminants or oxides can reduce contact resistance.
- Electrode Material Selection: Choosing the right electrode materials and coatings can also help minimize contact resistance and improve overall welding performance.
Contact resistance is a crucial factor to consider when using resistance spot welding machines. It can significantly impact the quality, efficiency, and maintenance requirements of the welding process. By understanding the effects of contact resistance and implementing appropriate measures to mitigate its influence, manufacturers can ensure consistent, high-quality welds in their products, ultimately contributing to the reliability and safety of the end result.