Resistance spot welding machines, commonly known as spot welders, are essential tools in various industries, including automotive, aerospace, and manufacturing. These machines play a crucial role in joining metal components together with precision and reliability. In this article, we will explore the structure and production characteristics of resistance spot welding machines.
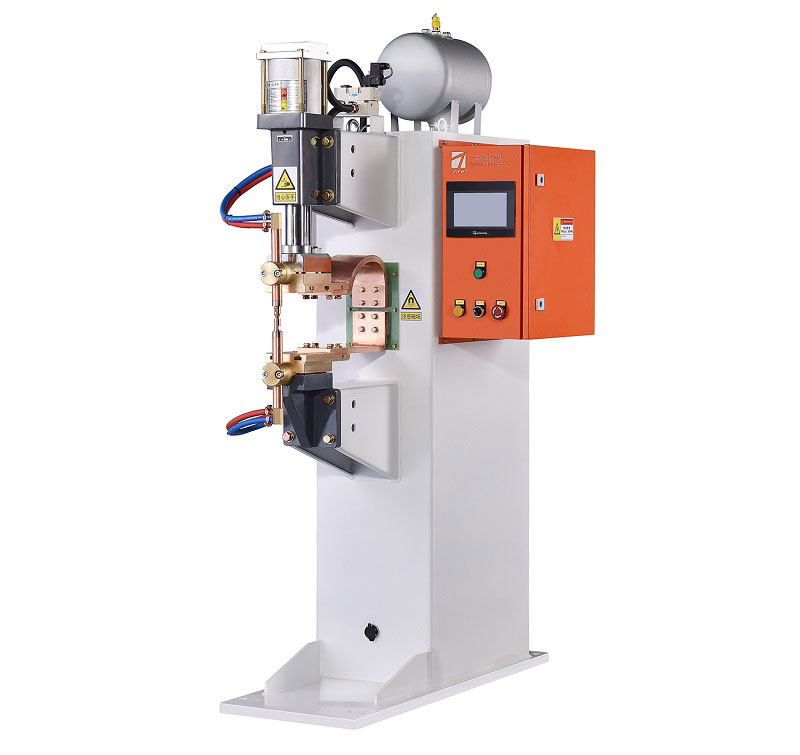
Structure of Resistance Spot Welding Machines:
Resistance spot welding machines consist of several key components that work together to create strong and durable welds:
- Welding Electrodes: These are the parts of the machine that come into direct contact with the metal pieces being joined. One electrode is stationary, while the other is movable and exerts pressure on the workpieces during welding.
- Power Supply: Spot welders are powered by electrical sources, typically alternating current (AC) or direct current (DC). The power supply provides the necessary energy for welding by passing an electrical current through the workpieces.
- Control System: Modern spot welders are equipped with advanced control systems that allow operators to precisely adjust welding parameters such as current, voltage, and welding time. This control ensures consistent and high-quality welds.
- Cooling System: During welding, a significant amount of heat is generated. To prevent overheating and maintain the machine’s efficiency, spot welders are equipped with cooling systems, which may involve water or air cooling.
Production Characteristics:
The production characteristics of resistance spot welding machines make them suitable for a wide range of manufacturing applications:
- Speed and Efficiency: Resistance spot welding is a fast and efficient welding process. It can create a weld in a fraction of a second, making it ideal for high-volume production lines.
- High Precision: The controlled and localized nature of spot welding ensures precise and consistent welds. This precision is crucial in industries where safety and quality standards are paramount.
- Versatility: Spot welders can join various metals, including steel, aluminum, and copper. They are commonly used in automotive assembly lines for joining sheet metal components.
- Minimal Distortion: Unlike some other welding techniques, resistance spot welding produces minimal distortion in the workpieces. This is essential for maintaining the integrity and appearance of the finished product.
- Strength and Reliability: Spot welds are known for their strength and reliability. They provide excellent structural integrity, making them suitable for critical applications.
- Environmental Benefits: Spot welding is a clean process with no emissions of harmful fumes or gases, making it environmentally friendly.
In conclusion, resistance spot welding machines are indispensable tools in modern manufacturing. Their robust structure and production characteristics make them a preferred choice for industries where precision, speed, and reliability are essential. Whether in automotive production or aerospace manufacturing, these machines continue to play a vital role in ensuring the integrity of welded joints and the quality of finished products.