Current control is a critical aspect of nut spot welding machines, as it directly influences the quality and reliability of the welds produced. This article aims to explore the strength of current control in nut spot welding machines and its impact on the welding process. By understanding the significance of precise current control, users can optimize their welding operations and achieve superior results in nut spot welding applications.
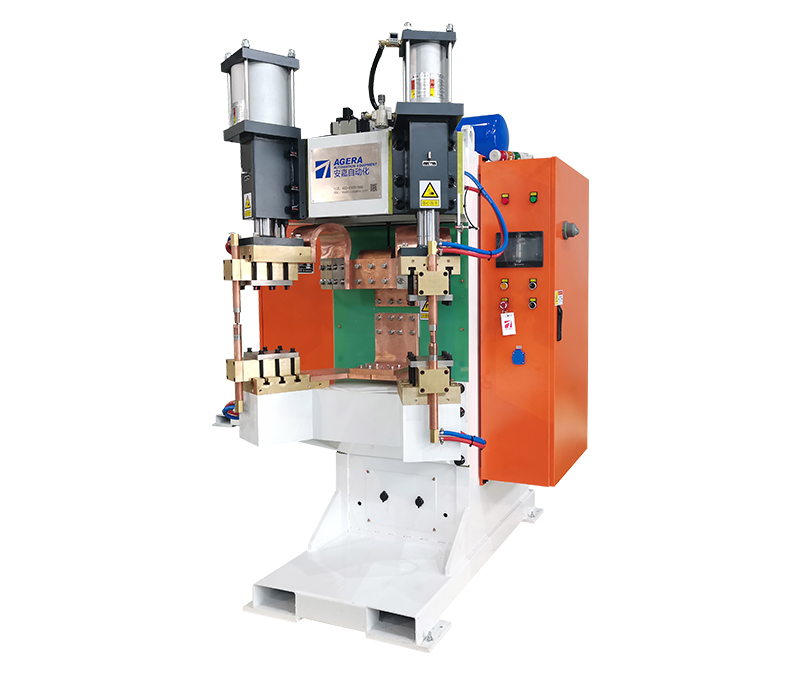
- Importance of Current Control: In nut spot welding, the strength of the current control plays a crucial role in achieving consistent and robust welds. Proper control of the welding current ensures adequate heat generation, which is necessary for effective fusion of the nut and the workpiece. Insufficient current may result in weak welds with insufficient penetration, while excessive current can lead to overheating, distortion, and even damage to the materials involved.
- Precision and Accuracy: To ensure optimal weld quality, nut spot welding machines must provide precise and accurate current control. This involves maintaining a stable and controlled current flow throughout the welding process. Modern welding machines utilize advanced control mechanisms, such as microprocessors and feedback systems, to monitor and adjust the current levels in real-time. This enables users to achieve consistent and repeatable welds, even when dealing with variations in material thickness or electrical resistivity.
- Current Monitoring and Regulation: Nut spot welding machines employ various techniques to monitor and regulate the welding current. These include current sensors, closed-loop feedback systems, and programmable control interfaces. Current sensors measure the actual current flowing through the welding circuit, allowing the machine to adjust and maintain the desired current level. Closed-loop feedback systems continuously compare the measured current with the setpoint and make necessary adjustments to ensure precise control. Programmable control interfaces enable users to define and fine-tune the current parameters according to the specific welding requirements.
- Pulse Current Control: Many advanced nut spot welding machines utilize pulse current control techniques. Instead of providing a continuous current flow, these machines deliver short pulses of high current followed by controlled rest periods. Pulse current control offers several advantages, including reduced heat input, improved control over nugget formation, and minimized thermal distortion. This technique allows for efficient energy transfer while mitigating the risks of material overheating and excessive spatter.
- Customization and Adaptability: To cater to various nut spot welding applications, modern machines offer customization options for current control. Users can adjust parameters such as peak current, duration of pulses, and rest periods to optimize the weld quality based on the specific requirements of the materials and joint configurations. This flexibility ensures that the welding process can be tailored to achieve optimal results across a wide range of nut spot welding applications.
The strength of current control in nut spot welding machines is crucial for producing reliable and high-quality welds. Precise current control ensures proper heat generation, resulting in strong and durable connections between nuts and workpieces. By utilizing advanced current monitoring and regulation techniques, such as pulse current control, users can achieve consistent and repeatable welds while minimizing thermal distortion and material damage. Customization options further enhance the adaptability of nut spot welding machines, allowing for optimal performance in various applications. Understanding and harnessing the strength of current control empowers users to achieve superior results in nut spot welding operations.