Shunting, or the undesired current flow through unintended paths, can significantly affect the performance and quality of energy storage spot welding machines. Minimizing shunting is crucial for achieving reliable and efficient welding operations. This article explores various strategies to reduce shunting in energy storage spot welding machines.
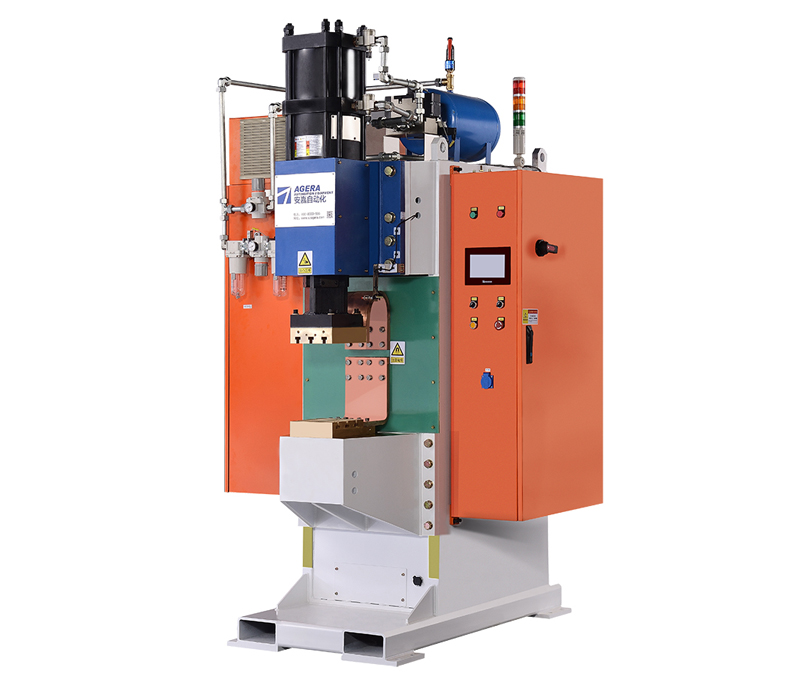
- Electrode Alignment and Pressure: Proper alignment and sufficient pressure between the electrodes and the workpiece are essential to minimize shunting. When the electrodes are misaligned or uneven pressure is applied, gaps or insufficient contact can occur, leading to increased resistance and potential shunting. Regular maintenance and inspection of the electrodes, ensuring they are properly aligned and applying consistent pressure, can help reduce shunting.
- Electrode Maintenance: Regular electrode maintenance is crucial for preventing shunting. Over time, electrodes can develop surface contaminants such as oxides, coatings, or debris, which increase electrical resistance and contribute to shunting. Cleaning and polishing the electrode surfaces, as well as ensuring proper tip geometry, can help maintain optimal electrical contact and minimize shunting.
- Electrode Material Selection: Choosing suitable electrode materials is another factor in reducing shunting. Certain electrode materials have lower resistivity, promoting better electrical conductivity and minimizing shunting. Copper and its alloys are commonly used electrode materials due to their excellent electrical and thermal conductivity properties. Proper electrode material selection can help reduce resistance and minimize shunting.
- Welding Parameter Optimization: Optimizing welding parameters can also contribute to reducing shunting. Parameters such as welding current, pulse duration, and weld time should be set within the recommended range for the specific materials and thicknesses being welded. Excessive current or prolonged weld times can increase resistance and lead to shunting. By carefully adjusting and optimizing welding parameters, users can minimize shunting and improve welding quality.
- Control System Calibration: Regular calibration of the control system is essential to maintain accurate and precise control over the welding process. Inaccurate control system settings can result in inconsistent welds, leading to increased resistance and potential shunting. Calibrating the control system according to the manufacturer’s guidelines ensures proper synchronization between the energy storage system, weld control, and electrode actuation, reducing the likelihood of shunting.
Reducing shunting in energy storage spot welding machines is vital for achieving high-quality and reliable welds. By implementing strategies such as ensuring proper electrode alignment and pressure, conducting regular electrode maintenance, selecting suitable electrode materials, optimizing welding parameters, and calibrating the control system, users can minimize shunting and improve the overall welding performance. These measures contribute to enhanced efficiency, reduced energy losses, and improved weld quality in energy storage spot welding applications.