The quality of butt welding machine processes is of paramount importance to ensure the reliability and durability of welded joints. Establishing and adhering to rigorous process standards is crucial for achieving consistent weld results. This article explores the essential quality standards that govern butt welding machine processes and their significance in ensuring weld integrity and performance.
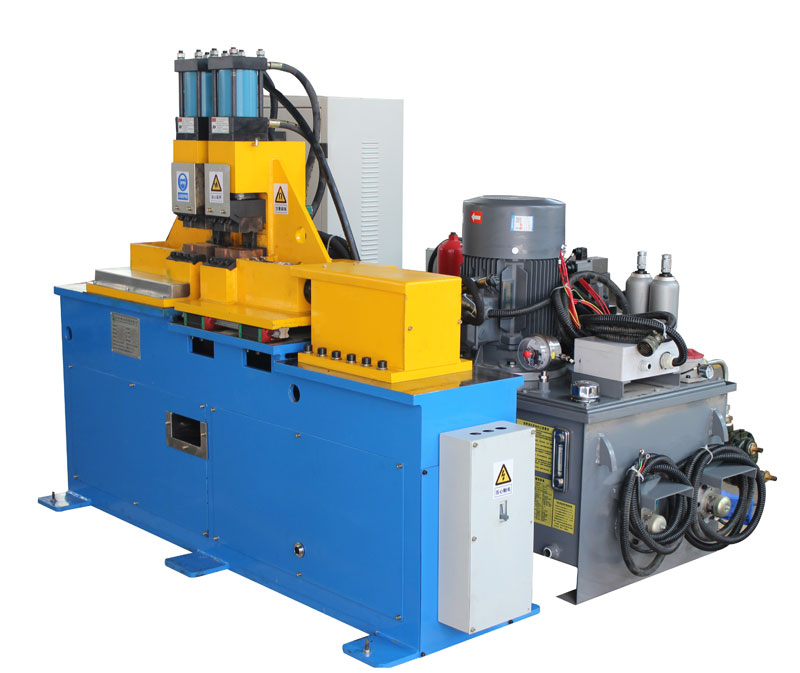
- Definition of Quality Standards: Quality standards in butt welding machines encompass a set of predefined guidelines and procedures that govern the welding process. These standards address various aspects, including material selection, welding parameters, equipment calibration, and inspection criteria.
- International Welding Standards: Internationally recognized welding standards, such as those issued by the American Welding Society (AWS) or the International Organization for Standardization (ISO), provide comprehensive guidelines for welding processes. These standards cover a wide range of welding procedures, from welding process selection to welder qualification, and are crucial for ensuring the overall quality of welded joints.
- Material Specification and Preparation: Quality standards dictate the specific materials suitable for welding and provide guidelines for their proper preparation. Material cleanliness, joint design, and surface preparation are essential aspects that influence weld quality and adherence to quality standards.
- Welding Parameters and Controls: The welding process relies on various parameters, such as welding current, voltage, welding speed, and electrode force. Quality standards establish acceptable ranges for these parameters, ensuring that the welding process remains within safe and optimal operating conditions.
- Non-Destructive Testing (NDT) and Inspection: NDT methods, like ultrasonic testing and radiography, are critical for assessing weld integrity without damaging the workpiece. Quality standards define the type and frequency of NDT required for specific welding applications to verify weld quality and compliance.
- Documentation and Traceability: Maintaining comprehensive documentation of the welding process, including materials used, welding parameters, and inspection results, is an integral part of quality standards. Proper documentation ensures traceability and enables audits for process validation and continuous improvement.
- Welder Qualification and Training: Quality standards also cover welder qualification and training requirements. Welders must undergo testing and certification processes to demonstrate their competency in performing specific welding procedures.
In conclusion, adhering to stringent quality standards is essential for butt welding machines to produce reliable and high-quality welds. By following internationally recognized welding standards and guidelines, manufacturers can ensure consistent weld integrity and performance. Proper material preparation, welding parameter control, non-destructive testing, and documentation play crucial roles in meeting the established quality standards. Welder qualification and ongoing training further contribute to the overall quality and efficiency of the welding process. Emphasizing the importance of quality standards ensures that butt welding machines produce welds that meet industry demands and customer expectations.