Resistance welding is a widely used manufacturing process, known for its efficiency and reliability in joining metals. Ensuring the quality of welded components is crucial in various industries, from automotive to aerospace. In this article, we will discuss the key aspects of inspecting the welding quality of resistance welding machines.
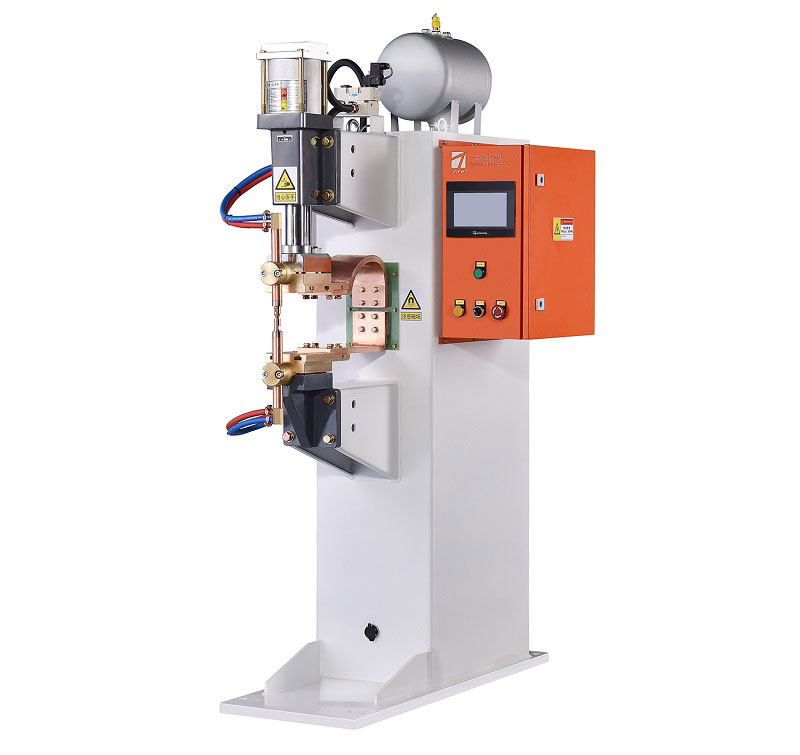
- Visual Inspection: The first step in quality control is a visual inspection of the welded joints. Inspectors look for irregularities such as cracks, voids, or incomplete fusion. Weld seams should be smooth and free from any surface defects.
- Dimensional Inspection: Precision is paramount in many applications, so measuring the dimensions of the welded area is critical. This ensures that the final product conforms to specifications.
- Weld Strength Testing: The strength of a weld is a fundamental quality parameter. This can be assessed through destructive or non-destructive testing methods, including tensile, bend, or shear testing.
- Ultrasonic Testing: For non-destructive evaluation, ultrasonic testing is commonly employed. It uses high-frequency sound waves to detect internal defects or inconsistencies within the weld.
- Radiographic Inspection: Radiography is another non-destructive technique that provides a detailed view of the weld’s internal structure. It is especially useful for thicker materials or critical applications.
- Macroscopic Examination: This involves cross-sectioning a sample of the weld to examine its internal structure under a microscope. It helps identify issues such as improper penetration or excessive porosity.
- Welding Process Monitoring: Many modern resistance welding machines are equipped with sensors and monitoring systems that continuously track parameters like current, voltage, and welding time. Deviations from set values can indicate welding quality issues.
- Electrode Maintenance: Regular inspection and maintenance of welding electrodes are essential. Worn or damaged electrodes can result in poor weld quality.
- Quality Documentation: Keeping detailed records of all welding parameters and inspection results is crucial for traceability and process improvement.
- Operator Training: Skilled operators play a vital role in maintaining welding quality. Proper training and certification programs ensure that operators understand the welding process and can troubleshoot issues.
In conclusion, ensuring the quality of resistance welding machine outputs is essential to meet industry standards and produce reliable products. A combination of visual inspections, various testing methods, and a focus on process control and maintenance helps achieve consistent, high-quality welds. Investing in quality control not only reduces defects and rework but also enhances the overall safety and performance of welded components in diverse applications.