Spatter, the undesired projection of molten metal particles during the welding process, can affect the quality, cleanliness, and safety of nut welding operations. This article discusses effective strategies to minimize spatter in nut welding machines, ensuring cleaner and more efficient welds.
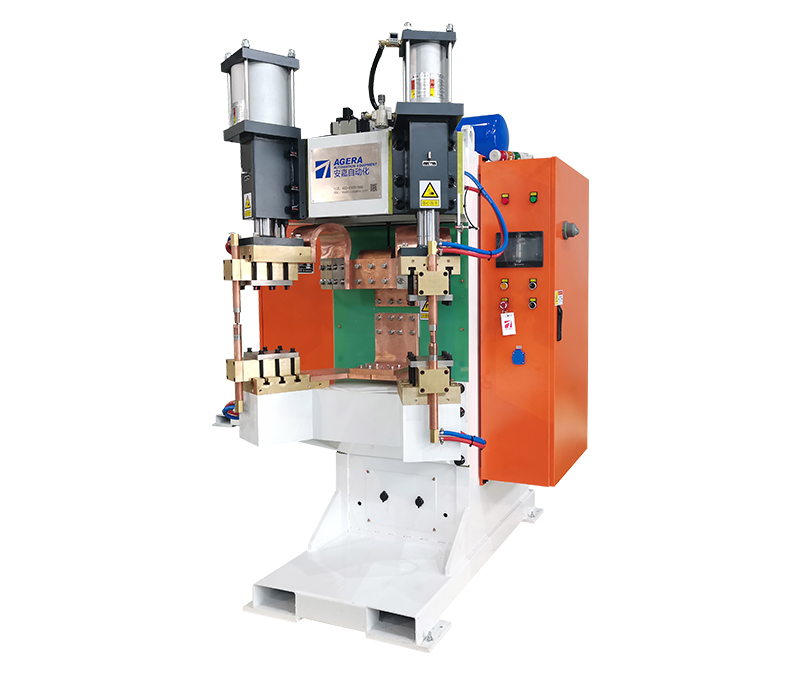
- Optimize Welding Parameters:
- Ensure proper selection of welding parameters, including voltage, current, and welding speed.
- Adjust the parameters to achieve the ideal balance between heat input and material deposition, reducing the likelihood of excessive spatter.
- Use Anti-Spatter Agents:
- Apply anti-spatter agents or coatings on the welding surfaces and surrounding areas.
- These agents create a protective barrier that prevents spatter from adhering to the workpiece, reducing the occurrence of spatter and simplifying post-weld cleanup.
- Electrode Selection:
- Choose appropriate electrode types and sizes based on the specific welding application.
- Certain electrode compositions and coatings can help minimize spatter formation and improve overall weld quality.
- Consult with electrode manufacturers or welding experts to select the most suitable electrodes for your nut welding machine.
- Maintain Proper Shielding Gas Flow:
- Ensure a consistent and adequate flow of shielding gas during the welding process.
- Shielding gas, such as argon or a mixture of gases, creates a protective atmosphere around the weld area, minimizing oxidation and spatter formation.
- Regularly check gas flow rates, gas purity, and gas nozzle condition to maintain optimal shielding gas coverage.
- Control Welding Technique:
- Adopt proper welding techniques, such as maintaining the correct arc length and travel speed.
- Consistent and steady movements can help control the heat input and reduce spatter generation.
- Avoid excessive weaving or erratic movements that can contribute to spatter formation.
- Maintain Clean Workpiece Surface:
- Ensure the workpiece surfaces are clean and free from contaminants, such as rust, oil, or debris.
- Dirty or contaminated surfaces can lead to increased spatter and compromised weld quality.
- Clean the workpieces thoroughly before welding, using appropriate cleaning methods and solvents.
Minimizing spatter in nut welding machines is crucial for achieving high-quality welds and improving operational efficiency. By optimizing welding parameters, using anti-spatter agents, selecting suitable electrodes, maintaining proper shielding gas flow, controlling welding techniques, and ensuring clean workpiece surfaces, operators can effectively reduce spatter formation. Implementing these strategies not only improves the overall welding process but also enhances the safety and reliability of nut welding operations.