Deformation is a common concern in nut spot welding, as the welded components may undergo unwanted shape changes during the process. However, by implementing effective techniques and following best practices, it is possible to minimize and prevent deformation in nut spot welding. This article explores various strategies to achieve distortion-free welds and maintain the structural integrity of the workpieces.
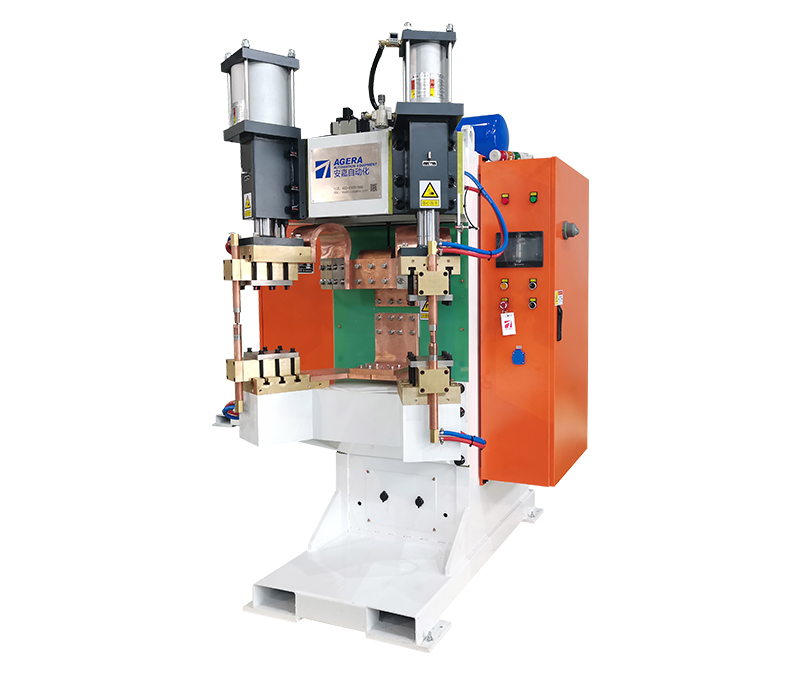
- Proper Welding Sequence: To prevent deformation, it is crucial to establish a well-planned welding sequence. Start welding from the center and progress outward, allowing for gradual cooling and stress distribution throughout the workpiece.
- Material Selection: Choosing materials with compatible thermal expansion coefficients can help reduce the risk of deformation. Avoid welding dissimilar materials with significantly different properties to maintain uniformity during heating and cooling.
- Optimal Welding Parameters: Calibrate the welding parameters based on the material thickness and joint design. Ensuring consistent and appropriate current, time, and pressure will help achieve a balanced heat distribution and minimize distortion.
- Workpiece Fixturing: Proper fixturing and clamping are essential to maintain workpiece stability during welding. Securely hold the components in place to avoid movement and distortion during the welding process.
- Preheating: In certain cases, preheating the workpieces can be beneficial. Preheating helps reduce the temperature gradient between the weld area and the surrounding material, thus minimizing thermal shock and deformation.
- Welding Speed: Controlling the welding speed is crucial in preventing deformation. A balanced and steady welding speed allows for uniform heat input and reduces the risk of localized overheating.
- Post-Weld Heat Treatment: Consider post-weld heat treatment to relieve residual stresses and further stabilize the welded joint, which can help prevent deformation over time.
- Controlled Cooling: Implement controlled cooling methods to reduce the risk of rapid cooling-induced deformation. Slow and uniform cooling can be achieved by using insulating materials or temperature-controlled environments.
Preventing deformation in nut spot welding requires a comprehensive approach that encompasses material selection, proper fixturing, optimal welding parameters, and controlled cooling techniques. By adhering to a well-planned welding sequence and considering preheating or post-weld heat treatment when necessary, operators can minimize thermal stresses and achieve distortion-free welds. Implementing these techniques will not only ensure the quality of the welded joints but also maintain the structural integrity of the components, making them suitable for a wide range of applications.