Resistance spot welding is a fundamental process in manufacturing, crucial for joining metal components in various industries. Before initiating the welding process, it’s essential to perform a series of preparatory tasks to ensure a successful and high-quality weld. In this article, we will outline the key steps required before using a resistance spot welding machine.
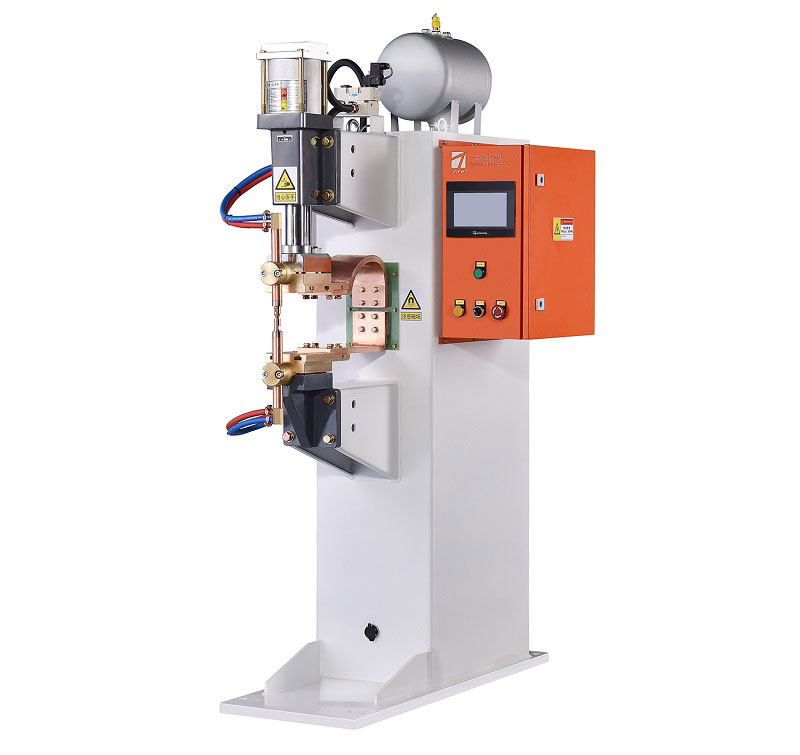
- Safety First: Safety is paramount in any welding operation. Before beginning, ensure that you are wearing appropriate personal protective equipment (PPE), including welding gloves, a welding helmet with a face shield, and flame-resistant clothing. Check the machine’s safety features and emergency shut-off procedures.
- Inspect the Machine: Examine the resistance spot welding machine for any signs of damage, wear, or malfunction. Inspect the electrodes, cables, and the welding gun. Ensure that all components are in good working condition.
- Select the Right Electrodes: The choice of electrodes plays a critical role in achieving a successful weld. Select the appropriate electrode material and shape for the specific metals you are welding. Ensure that the electrodes are clean and free from contaminants.
- Prepare the Workpieces: Properly prepare the metal workpieces to be welded. This includes cleaning the surfaces to remove any rust, paint, or debris. Properly align and secure the workpieces to ensure they do not shift during welding.
- Set the Welding Parameters: Consult the welding procedure specification (WPS) to determine the correct welding parameters, such as welding current, welding time, and electrode force. Set the machine to these parameters to achieve the desired weld quality.
- Check Power and Cooling: Ensure that the welding machine is adequately powered and connected to the appropriate electrical supply. Check the cooling system to prevent overheating during prolonged welding operations.
- Test Welds: Before beginning the actual production welding, perform a series of test welds on scrap pieces of metal. This helps to fine-tune the welding parameters and ensures that the machine is functioning correctly.
- Monitor the Environment: Welding produces fumes and gases that can be harmful if inhaled. Make sure the welding area is adequately ventilated, and if necessary, use fume extraction systems to remove harmful fumes from the workspace.
- Quality Control: Implement a quality control process to inspect the finished welds. This may include visual inspections, non-destructive testing, or destructive testing, depending on the application’s requirements.
- Documentation: Keep thorough records of the welding process, including welding parameters, inspection results, and any deviations from the established procedures. Proper documentation is essential for traceability and quality control.
In conclusion, proper preparation is key to successful resistance spot welding. By following these steps and adhering to safety guidelines, you can ensure that your welding operation is efficient, safe, and produces high-quality welds. Always remember that attention to detail in the preparation phase significantly contributes to the overall success of the welding process.