Compressed air is a vital component in the operation of nut welding machines, providing the necessary force and power for various pneumatic functions. However, it is essential to follow certain precautions to ensure the safe and efficient use of compressed air in nut welding machines. This article outlines important considerations and safety measures to be taken when dealing with compressed air supply in nut welding machine operations.
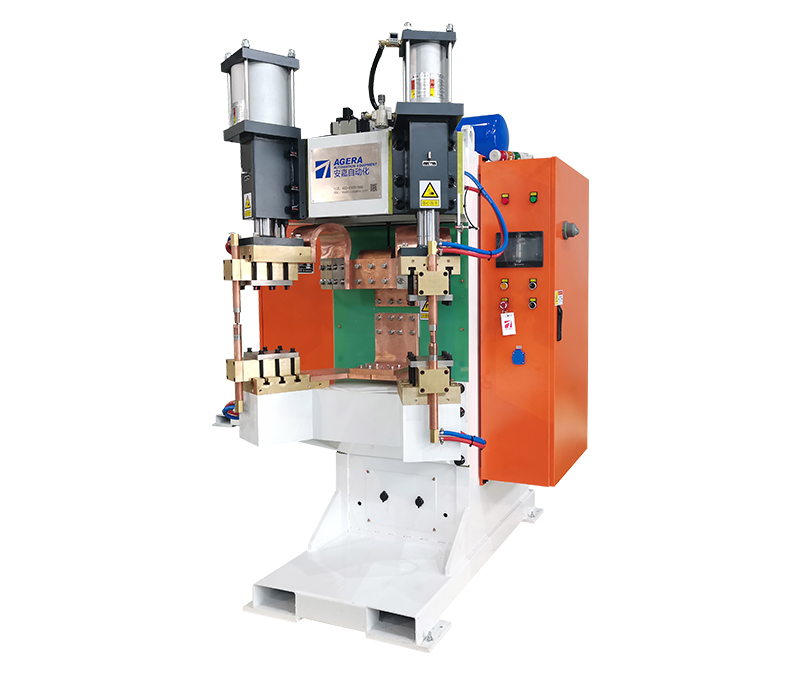
- Proper Installation: The compressed air supply system should be installed by qualified professionals following manufacturer guidelines and local regulations. Proper installation includes using suitable piping materials, ensuring proper fittings and connections, and implementing appropriate pressure regulation mechanisms.
- Adequate Pressure Regulation: Maintaining the correct air pressure is crucial for the safe and optimal operation of nut welding machines. The air pressure should be regulated within the recommended range specified by the machine manufacturer. Excessive pressure can lead to equipment damage, while inadequate pressure can result in compromised welding quality and performance.
- Regular Inspection and Maintenance: Regular inspection and maintenance of the compressed air system are necessary to identify and address potential issues. This includes checking for leaks, ensuring proper filtration to remove contaminants, and verifying the integrity of pressure gauges and control valves. Any abnormalities or malfunctions should be promptly addressed by qualified technicians.
- Proper Filtration: Compressed air used in nut welding machines should be adequately filtered to remove moisture, oil, and other contaminants. Proper filtration helps prevent damage to pneumatic components, improves the longevity of equipment, and ensures consistent welding quality. Regular maintenance of filters is essential to prevent clogging and maintain optimal filtration efficiency.
- Safety Valves and Pressure Relief Devices: In case of excessive pressure buildup, safety valves and pressure relief devices are crucial to prevent equipment failure and protect against potential hazards. These safety mechanisms should be properly installed, regularly inspected, and tested to ensure they are functioning correctly.
- Operator Training and Awareness: Operators should receive proper training on the safe use and handling of compressed air in nut welding machines. They should be aware of the potential hazards associated with compressed air systems and understand the importance of adhering to safety protocols. Operators should also be trained to recognize signs of air system malfunction, such as unusual noises, pressure fluctuations, or leaks, and know how to respond appropriately.
- Emergency Shutdown Procedures: Clear emergency shutdown procedures should be in place in the event of a compressed air system failure or other emergencies. Operators should be trained on these procedures and know how to safely shut down the system in case of an emergency.
Ensuring the safe and efficient use of compressed air in nut welding machine operations is essential for operator safety and equipment performance. By following proper installation practices, regulating air pressure, conducting regular inspection and maintenance, implementing proper filtration, utilizing safety valves and relief devices, providing operator training, and establishing emergency shutdown procedures, the risks associated with compressed air can be mitigated. Adhering to these precautions not only promotes a safe working environment but also contributes to the overall reliability and productivity of nut welding processes.