After completing welding operations with butt welding machines, thorough post-weld cleaning is essential to ensure the quality and longevity of the welded joints. This article delves into the specific cleaning requirements that follow butt welding processes, emphasizing the significance of proper cleaning procedures for maintaining weld integrity and safety.
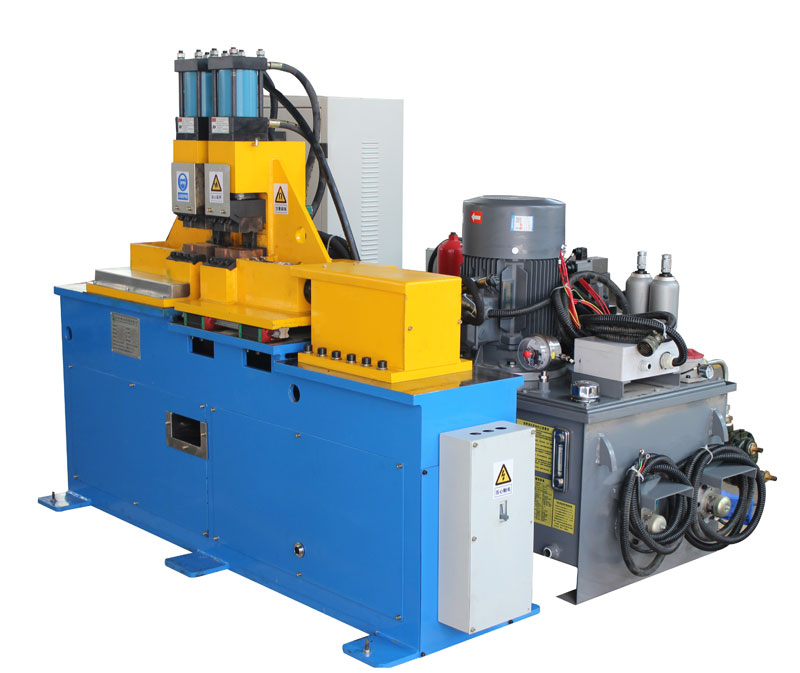
- Removal of Weld Spatter and Slag: One of the primary cleaning tasks is the removal of weld spatter and slag. During the welding process, metal spatter can be expelled onto the workpiece surface, and slag may form on the weld bead. These remnants must be diligently removed using appropriate tools, such as wire brushes or chipping hammers, to avoid potential issues like porosity or compromised joint strength.
- Cleaning of Welding Fixtures and Electrodes: Welding fixtures and electrodes can accumulate debris and contamination during the welding process. Proper cleaning of these components is crucial to maintain consistent welding quality. Regular inspection and cleaning of the fixtures and electrodes help prevent interference during subsequent welding operations.
- Surface Cleaning for Inspection: Post-weld cleaning should include thorough surface cleaning to facilitate inspection and ensure the quality of the welds. Cleaning agents like solvents or degreasers may be used to remove any residues, oils, or grease from the weld area, providing a clear view for weld inspection and testing.
- Deburring and Smoothing Weld Beads: In some cases, weld beads may require deburring and smoothing to achieve the desired finish and appearance. Proper deburring helps eliminate sharp edges and uneven surfaces that could lead to stress concentration and potential failure.
- Verification of Weld Dimensions: Post-weld cleaning provides an opportunity to verify weld dimensions and adherence to specified tolerances. Measuring tools, such as calipers or micrometers, can be employed to confirm that the weld meets the required dimensional standards.
- Removal of Protective Coatings: If the workpiece was coated with protective substances before welding, such as paint or anti-corrosion coatings, they must be removed from the welding area. Residual coatings can negatively affect the weld’s integrity and should be eliminated before proceeding with any additional surface treatments or applications.
In conclusion, post-weld cleaning is a critical aspect of the welding process with butt welding machines. Proper cleaning procedures, including the removal of weld spatter, slag, and contaminants, ensure the weld’s integrity, safety, and appearance. Regular cleaning and maintenance of welding fixtures and electrodes further contribute to consistent welding quality. By adhering to these cleaning requirements, welders can achieve reliable and durable welded joints that meet stringent industry standards and customer expectations.