Determining the appropriate protrusion length for workpieces in butt welding machines is crucial for achieving successful and high-quality welds. The protrusion length refers to the extension of the workpieces beyond the clamping mechanism during welding. This article explores the significance of selecting the optimal protrusion length, highlighting its impact on welding efficiency, joint integrity, and overall welding performance.
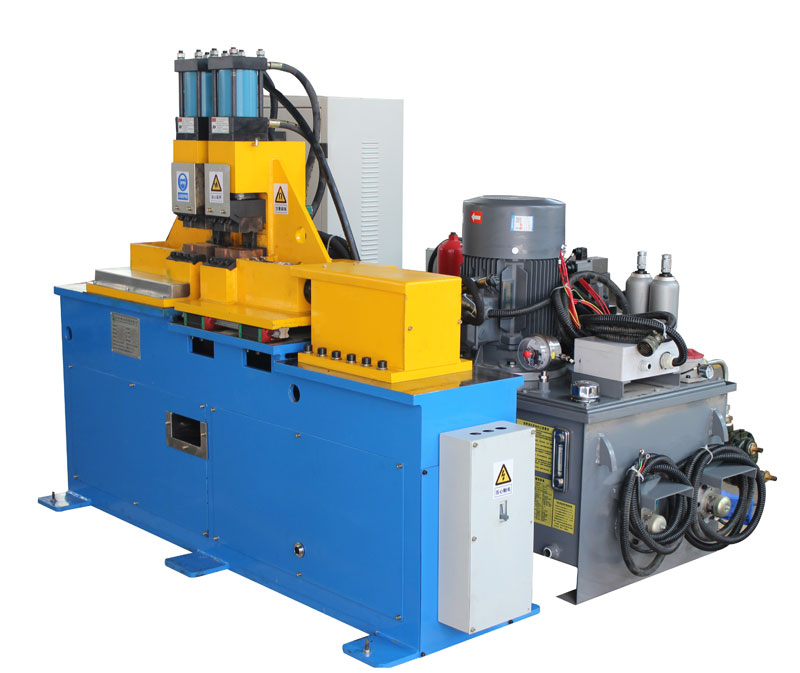
Optimal Protrusion Length for Butt Welding Machine Workpieces:
- Joint Accessibility: The protrusion length should be sufficient to provide easy access to the joint area for electrode insertion and welding. A proper protrusion length ensures that the welding electrode can reach the root of the joint effectively, promoting adequate fusion and penetration.
- Effective Heat Distribution: An appropriate protrusion length contributes to uniform heat distribution along the joint interface. Proper heat distribution is essential for ensuring consistent weld bead formation and avoiding overheating or underheating of the workpieces.
- Welding Parameter Adjustment: The protrusion length may need adjustment based on the welding parameters, such as welding current and voltage, and the material thickness. Different materials and joint configurations may require specific protrusion lengths to achieve optimal weld quality.
- Workpiece Thickness: The thickness of the workpieces is a critical factor in determining the protrusion length. Thicker workpieces generally require a longer protrusion to allow sufficient heat penetration and fusion at the joint.
- Clamping Stability: While an appropriate protrusion length is essential, care must be taken not to exceed the clamping mechanism’s capacity. Maintaining stable clamping throughout the welding process is vital for joint alignment and weld integrity.
- Welding Position and Technique: The welding position and technique used can influence the ideal protrusion length. For instance, vertical or overhead welding may require shorter protrusion lengths to minimize the risk of sagging or distortion during the weld.
In conclusion, selecting the optimal protrusion length for workpieces in butt welding machines is a critical consideration for welders and professionals. The protrusion length impacts joint accessibility, heat distribution, welding parameter adjustment, workpiece thickness, clamping stability, and welding position. Understanding the significance of the protrusion length empowers welders to optimize welding processes, ensuring uniform weld quality, and achieving reliable joint integrity. Emphasizing the importance of this parameter supports advancements in welding technology, promoting excellence in metal joining across diverse industrial applications.