Welding spatter is a common issue in energy storage spot welding machines that can lead to weld defects, equipment contamination, and increased post-weld cleaning efforts. Effectively managing and minimizing welding spatter is crucial for achieving high-quality welds and improving the overall welding process. This article focuses on the strategies and techniques to avoid or reduce welding spatter in energy storage spot welding machines.
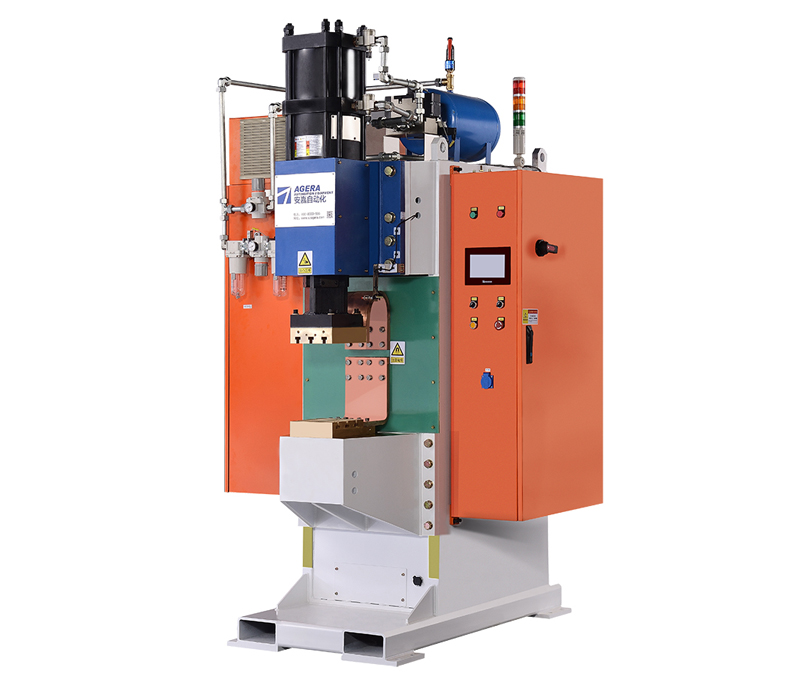
- Electrode Condition and Alignment: Maintaining the electrodes in good condition is essential for minimizing welding spatter. Damaged or worn-out electrodes can result in uneven current distribution, leading to increased spatter. Regularly inspecting and replacing worn electrodes ensures proper contact and reduces the likelihood of spatter. Additionally, ensuring accurate alignment between the electrodes and workpieces promotes stable arc formation and reduces spatter.
- Proper Material Preparation: Effective material preparation plays a significant role in spatter reduction. Before welding, it is crucial to clean and degrease the workpiece surfaces to remove any contaminants or coatings that can contribute to spatter. Additionally, ensuring proper fit-up and alignment between the workpieces minimizes gaps and irregularities that can lead to spatter formation.
- Optimal Welding Parameters: Adjusting the welding parameters can help control spatter generation. Parameters such as welding current, voltage, and duration should be set within the recommended range for the specific material and thickness being welded. Using higher welding currents can lead to excessive spatter, while lower currents may result in poor fusion. Finding the optimal balance of parameters is key to minimizing spatter.
- Gas Shielding: Utilizing an appropriate gas shielding technique is crucial for reducing spatter in energy storage spot welding machines. Inert gases, such as argon or helium, are commonly used to create a protective atmosphere around the weld pool, preventing atmospheric contamination and reducing spatter. Proper gas flow rate and distribution ensure sufficient coverage and minimize spatter formation.
- Pulse Welding Technique: Implementing pulse welding techniques can effectively reduce spatter. Pulse welding involves alternating high and low currents during the welding process, which helps control heat input and reduces spatter formation. The pulsing action allows for better control over the molten metal transfer, resulting in smoother welds with reduced spatter.
Welding spatter can be a challenge in energy storage spot welding machines, but by implementing appropriate strategies, it can be effectively mitigated. Maintaining electrode condition, proper material preparation, optimizing welding parameters, utilizing gas shielding, and employing pulse welding techniques are all important steps in reducing spatter. By implementing these measures, operators can achieve high-quality welds, minimize post-weld cleaning efforts, and improve overall welding efficiency in energy storage spot welding processes.