Welding is a critical process in various industries, ensuring the structural integrity and longevity of countless products. When it comes to nut spot welding machines, maintaining high welding quality is of utmost importance. In this article, we will explore several methods to enhance the quality of welding in nut spot welding machines.
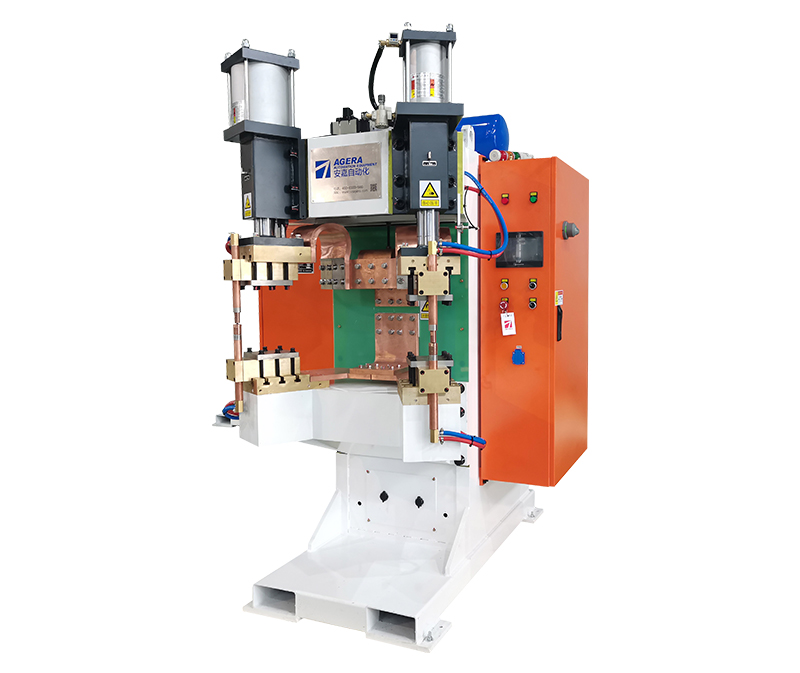
- Optimize Machine Settings: The first step in improving welding quality is to ensure that the nut spot welding machine is set up correctly. This includes adjusting parameters such as welding current, time, and pressure to match the specific material and thickness being welded. Proper setup helps create strong, consistent welds.
- Use High-Quality Electrodes: The quality of the welding electrodes is crucial. Ensure that you use high-quality, properly maintained electrodes to achieve clean and reliable welds. Worn or contaminated electrodes can lead to inconsistent welds and reduced quality.
- Regular Maintenance: Regular maintenance of the nut spot welding machine is essential. This includes cleaning and inspecting electrodes, checking cables and connections, and lubricating moving parts. Well-maintained machines perform more reliably and produce higher-quality welds.
- Material Preparation: Proper preparation of the materials being welded is vital. Surfaces should be clean and free from contaminants such as rust, grease, or paint. Additionally, aligning the materials accurately is essential for achieving precise and consistent welds.
- Quality Control and Testing: Implement a robust quality control and testing process. This can include non-destructive testing methods like visual inspection, ultrasonic testing, or X-rays to ensure the integrity of welds. Identifying defects early can prevent subpar products from reaching the market.
- Operator Training: Proper training for machine operators is key to achieving high welding quality. Operators should be knowledgeable about the machine’s operation and be able to recognize and address common welding issues.
- Automation: Consider automating the welding process wherever possible. Automated systems can consistently produce high-quality welds and reduce the chances of human error.
- Monitoring and Data Analysis: Implement monitoring systems that collect data during the welding process. Analyzing this data can help identify trends and potential issues, allowing for timely adjustments and improvements.
- Feedback Loop: Establish a feedback loop that involves the operators. Encourage them to report any issues or anomalies they encounter during the welding process. This feedback can be invaluable in continuously improving welding quality.
- Innovation and Technology: Stay updated with the latest welding technologies and innovations. New advancements can often lead to more efficient and higher-quality welding processes.
In conclusion, achieving high welding quality with nut spot welding machines requires a combination of proper machine setup, quality materials, maintenance, and skilled operators. By implementing these methods and continuously seeking ways to improve, you can enhance the quality of welds, leading to more reliable and durable products. High-quality welding is not just a goal; it’s a necessity in ensuring the safety and performance of the final product.