Nut spot welding machines are essential tools used for joining metal components through spot welding. This article explores the various methods of operating these machines to achieve efficient and high-quality welds.
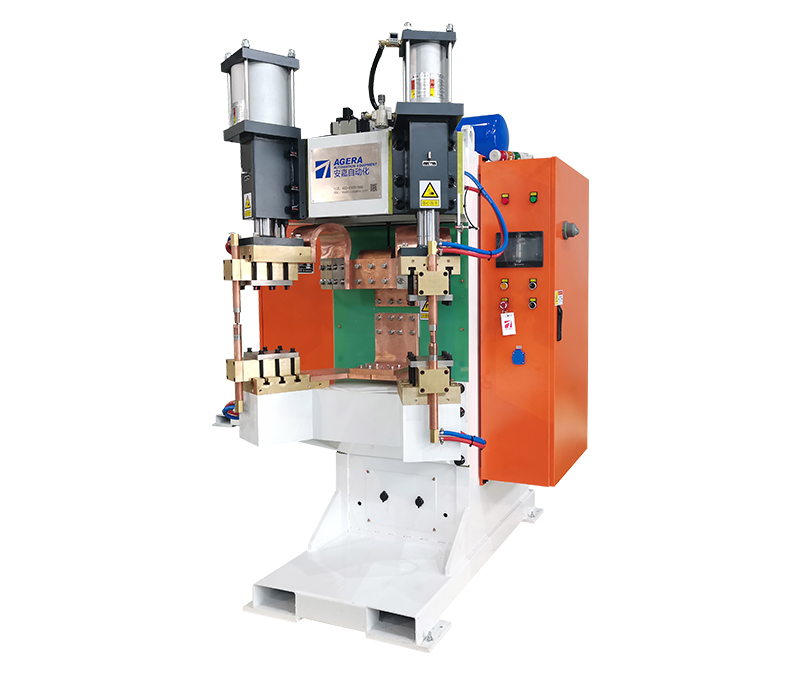
- Preparation: Before operating the nut spot welding machine, proper preparation is crucial. Ensure that the machine is in good working condition, and all safety measures are in place. Check the electrodes for wear and cleanliness, and ensure that the workpiece is securely positioned on the welding fixture.
- Selecting Welding Parameters: Adjusting the welding parameters is essential to achieve optimal weld quality. Factors such as welding current, welding time, and electrode pressure need to be set according to the material type, thickness, and desired weld spot size.
- Electrode Placement: Position the electrodes accurately on the workpiece, aligning them over the designated welding points. Ensure that the electrodes make good contact with the workpiece surface for effective heat transfer during welding.
- Triggering the Weld: Once the workpiece is properly positioned and the welding parameters are set, initiate the welding process by triggering the machine. The electrodes will apply pressure and electrical current to create a weld spot at the designated location.
- Cooling and Inspection: After the welding process is completed, allow the weld spot to cool before inspecting its quality. Check for any signs of defects or inadequate fusion. If necessary, conduct non-destructive testing to ensure the integrity of the weld joint.
- Repeat Welding Process: For multiple weld spots, repeat the welding process by repositioning the electrodes to the next welding points. Maintain consistency in welding parameters to ensure uniform weld quality across all spots.
- Post-Weld Treatment: Depending on the application, consider performing post-weld treatments such as annealing or stress-relief to improve the mechanical properties of the weld joints.
Operating a nut spot welding machine involves careful preparation, accurate electrode placement, and proper adjustment of welding parameters. By following these methods, operators can achieve reliable and high-quality welds, meeting the demands of various industrial applications. Additionally, regular maintenance of the machine and adherence to safety guidelines contribute to the longevity and efficiency of the welding process.