Resistance welding is a widely used manufacturing process that joins metals by applying pressure and passing a current through the materials to create a strong and reliable bond. Ensuring the quality of resistance welding machines is essential for maintaining product integrity and manufacturing efficiency. In this article, we will explore various methods and techniques to guarantee the quality of resistance welding machines.
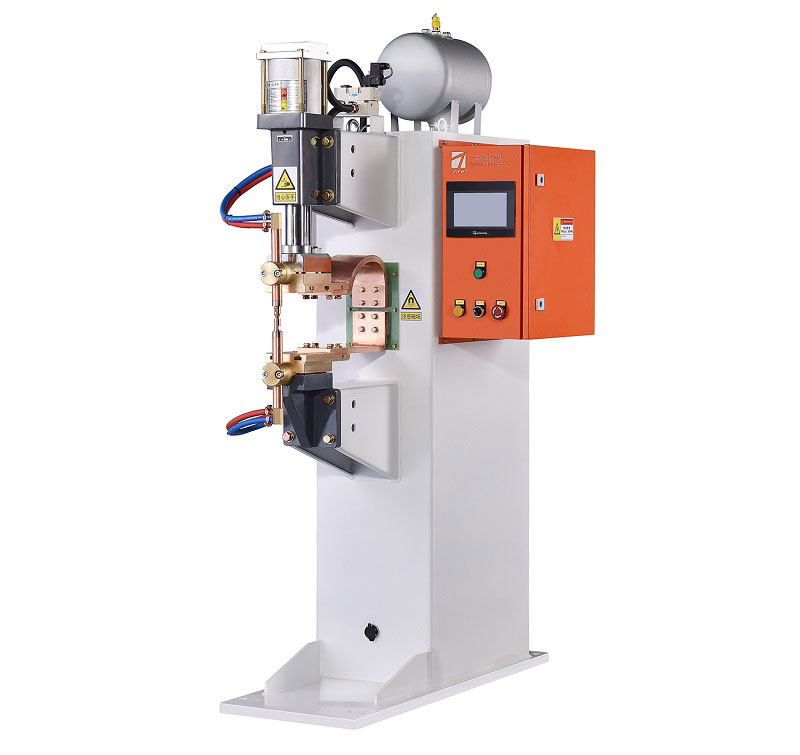
- Material Selection: The quality of the welding machine starts with selecting the right materials. High-quality alloys and components are essential for durability and performance. Ensure that the materials used in the construction of the machine meet industry standards.
- Design and Engineering: Proper design and engineering are crucial to the performance and reliability of a resistance welding machine. Work with experienced engineers who can design the machine to meet your specific welding requirements. The design should consider factors like the type of materials to be welded, the thickness of the materials, and the desired welding strength.
- Quality Control During Manufacturing: Implement strict quality control measures during the manufacturing process. Regular inspections and testing at various stages of production can help identify and address any issues before they affect the final product.
- Component Testing: Test critical components, such as transformers, electrodes, and control systems, to ensure they meet specifications. Any deviation from the desired performance should be addressed promptly.
- Welding Process Monitoring: Incorporate real-time monitoring systems into the welding process. These systems can detect variations and anomalies during welding, allowing for immediate adjustments and preventing defective welds.
- Operator Training: Well-trained operators are essential for maintaining the quality of the welding process. Provide comprehensive training programs to ensure that operators understand the equipment, safety procedures, and welding techniques.
- Regular Maintenance: Establish a routine maintenance schedule to keep the welding machine in optimal condition. Regular inspections, cleaning, and parts replacement are necessary to prevent breakdowns and maintain quality.
- Calibration and Certification: Periodically calibrate the welding machine to ensure it performs within specified tolerances. Certification by relevant authorities or organizations can provide assurance of quality and compliance with industry standards.
- Quality Documentation: Maintain detailed records of the machine’s maintenance, calibration, and performance. This documentation is essential for traceability and can help identify trends or issues over time.
- Continuous Improvement: Foster a culture of continuous improvement. Encourage feedback from operators and maintenance personnel, and use this information to make design or process improvements.
In conclusion, ensuring the quality of resistance welding machines is a multifaceted process that begins with material selection and extends throughout the entire lifecycle of the equipment. By focusing on design, quality control, regular maintenance, and operator training, manufacturers can produce high-quality welding machines that meet the demands of modern manufacturing.
By implementing these methods and techniques, manufacturers can not only enhance the performance and reliability of their resistance welding machines but also improve the overall quality of the products they produce. This, in turn, can lead to increased customer satisfaction and a stronger position in the market.