Resistance spot welding machines are widely used in various industries for joining metal components together. These machines rely heavily on the quality and condition of their electrodes for efficient and reliable performance. In this article, we will discuss the essential steps for maintaining the electrodes of a resistance spot welding machine.
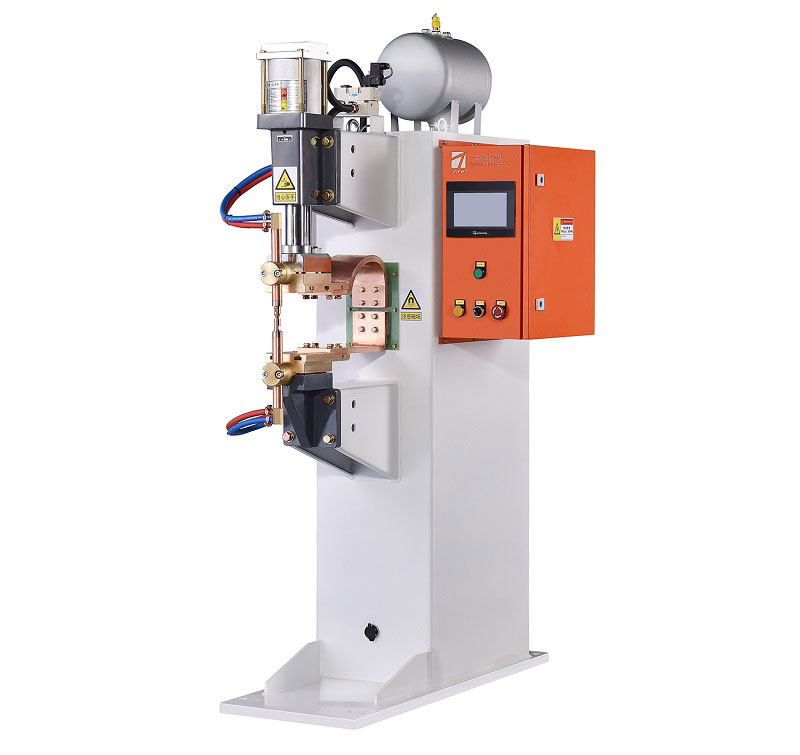
- Regular Inspection: Start by inspecting the electrodes regularly. Look for signs of wear, damage, or deformation. If you notice any issues, address them promptly to prevent further damage.
- Cleanliness Matters: Keep the electrodes clean. Contaminants such as rust, scale, or debris can affect the welding process. Clean the electrode tips thoroughly before and after each use.
- Proper Storage: When not in use, store the electrodes in a dry and clean environment. Consider using protective covers to prevent dust and moisture from accumulating on the electrode surfaces.
- Electrode Dressing: Periodically dress the electrode tips to remove any mushrooming or irregularities. This process ensures consistent contact and improves welding quality.
- Tip Dressing Technique: When dressing electrode tips, use the correct technique. Avoid over-dressing, as it can reduce the electrode’s lifespan. Follow the manufacturer’s recommendations for the dressing process.
- Cooling System Maintenance: If your welding machine has a water cooling system for the electrodes, make sure it is functioning correctly. Check for leaks, and replace or repair any damaged components promptly.
- Electrode Material: Ensure that the electrodes are made from the appropriate material for the job. Different materials are suitable for welding various metals. Consult your welding machine’s manual for guidance.
- Electrode Alignment: Proper alignment of the electrodes is crucial for consistent weld quality. Check and adjust the alignment as needed to maintain a precise welding process.
- Monitoring Electrode Life: Keep track of the electrode’s lifespan. Replace them when they reach the end of their service life to avoid poor weld quality and increased energy consumption.
- Training: Ensure that the operators are trained in electrode maintenance and replacement procedures. Proper training can extend electrode life and improve overall welding efficiency.
In conclusion, the maintenance of electrodes is a critical aspect of ensuring the longevity and performance of resistance spot welding machines. By following these guidelines, you can enhance the efficiency, consistency, and overall quality of your welding processes. Regular maintenance not only extends the lifespan of electrodes but also contributes to safer and more reliable welding operations.