Resistance spot welding is a widely used manufacturing process for joining metal components in various industries. However, like any mechanical system, it can encounter problems, and one common issue is the occurrence of cracks in the welding machine. In this article, we will explore the possible causes of this problem and discuss potential solutions.
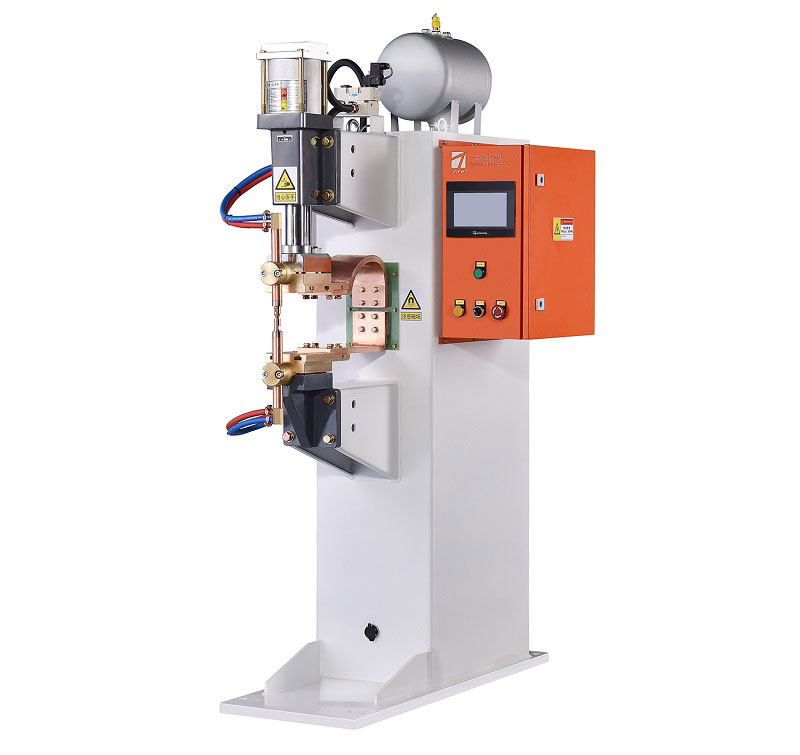
Causes of Cracking:
- Overheating: Excessive heat generated during the welding process can lead to the formation of cracks in the machine’s components. This heat buildup may be caused by prolonged use without adequate cooling or insufficient maintenance.
- Material Defects: Poor-quality materials used in the construction of the welding machine can be prone to cracking. These defects may not be immediately visible but can worsen over time due to stress and heat.
- Stress Concentration: Certain design flaws or uneven distribution of stress within the machine’s structure can create areas of stress concentration, making them more susceptible to cracking.
- Improper Usage: Incorrect operation of the machine, such as using the wrong settings, can result in excessive strain on its parts, leading to cracks over time.
Solutions:
- Regular Maintenance: Implement a routine maintenance schedule to inspect the machine for signs of wear and tear. Clean and lubricate moving parts as needed, and replace any damaged components promptly.
- Material Quality: Ensure that the welding machine is constructed using high-quality materials and components. This will minimize the risk of cracks forming due to material defects.
- Proper Cooling: Install effective cooling systems to prevent overheating during welding. Adequate cooling can significantly extend the lifespan of the machine.
- Operator Training: Properly train the machine operators to use the equipment correctly. Make sure they understand the settings and parameters needed for different welding tasks to avoid unnecessary stress on the machine.
- Design Analysis: Perform a stress analysis of the machine’s design to identify potential areas of stress concentration. Structural modifications may be necessary to distribute stress more evenly.
In conclusion, the issue of cracking in resistance spot welding machines can be addressed through a combination of proper maintenance, the use of high-quality materials, and operator training. By taking these steps, manufacturers can prolong the lifespan of their equipment, reduce downtime, and maintain the quality of their welding processes.