Welding speed is a critical parameter that directly affects the productivity and quality of nut welding operations. Achieving an optimal welding speed is essential to ensure efficient production while maintaining the desired weld characteristics. This article provides an overview of welding speed in nut welding machines, discussing its significance and factors that influence it. Understanding these aspects can help operators optimize their welding processes and achieve desirable outcomes.
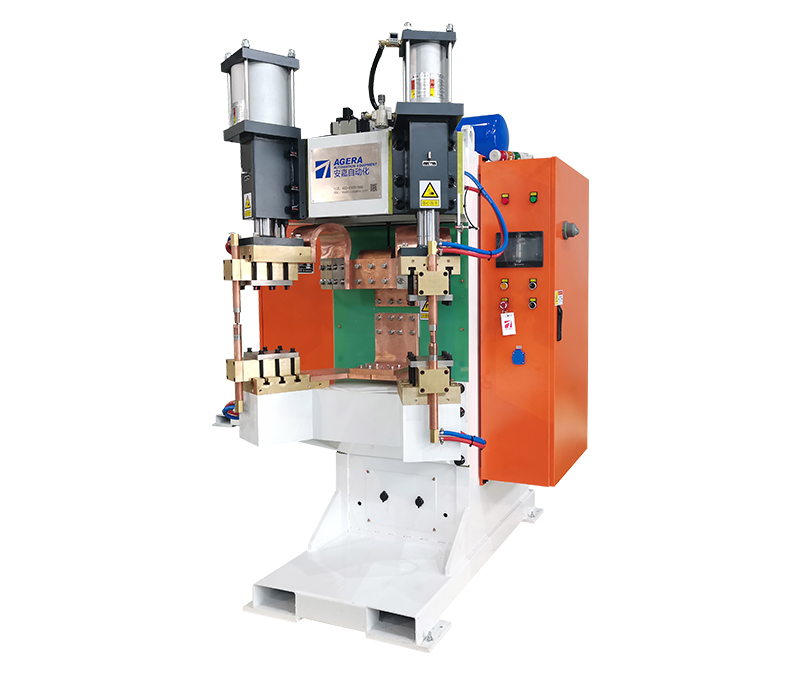
- Definition and Significance of Welding Speed: Welding speed refers to the rate at which the welding operation progresses along the joint or workpiece. It is typically measured in units of distance per unit of time, such as inches per minute or millimeters per second. The choice of welding speed is crucial as it directly impacts factors such as weld penetration, heat input, distortion, and overall productivity. Balancing the welding speed is essential to ensure proper fusion and achieve the desired weld quality.
- Factors Influencing Welding Speed: Several factors influence the optimal welding speed in nut welding machines. These include:
- Material Type: Different materials have varying thermal properties and welding characteristics, which can affect the suitable welding speed.
- Welding Technique: The chosen welding technique, such as resistance spot welding or projection welding, may have recommended speed ranges based on joint design and desired weld quality.
- Joint Configuration: The complexity and geometry of the joint can influence the welding speed. Factors such as joint thickness, accessibility, and fit-up affect the welding process.
- Power Source and Equipment: The performance capabilities of the welding machine, including the power source, control system, and electrode design, can impact the achievable welding speed.
- Welding Parameters: Factors such as current, voltage, electrode force, and cooling time need to be optimized in conjunction with the welding speed to maintain proper weld formation and avoid defects.
- Operator Skill and Experience: The proficiency of the operator in controlling the welding process, including maintaining a consistent speed, can significantly impact the overall welding speed.
- Balancing Productivity and Weld Quality: Finding the optimal welding speed involves striking a balance between productivity and weld quality. Increasing the welding speed can enhance productivity but may affect weld penetration and overall joint integrity. Conversely, reducing the speed may improve weld quality but could decrease productivity. Therefore, operators need to consider the specific requirements of each welding application and make adjustments accordingly.
Welding speed plays a crucial role in nut welding machines, directly influencing productivity and weld quality. Operators must carefully consider the material, joint configuration, equipment capabilities, and welding parameters to determine the optimal speed for each application. By striking the right balance between speed and weld quality, operators can achieve efficient and reliable nut welding operations.