Nut welding machines are equipped with cooling systems to manage the heat generated during welding operations. These cooling systems, including water cooling and air cooling, play a crucial role in maintaining the optimal operating temperature of the equipment. This article provides an overview of water cooling and air cooling systems in nut welding machines, highlighting their functions and benefits in ensuring efficient and reliable welding processes.
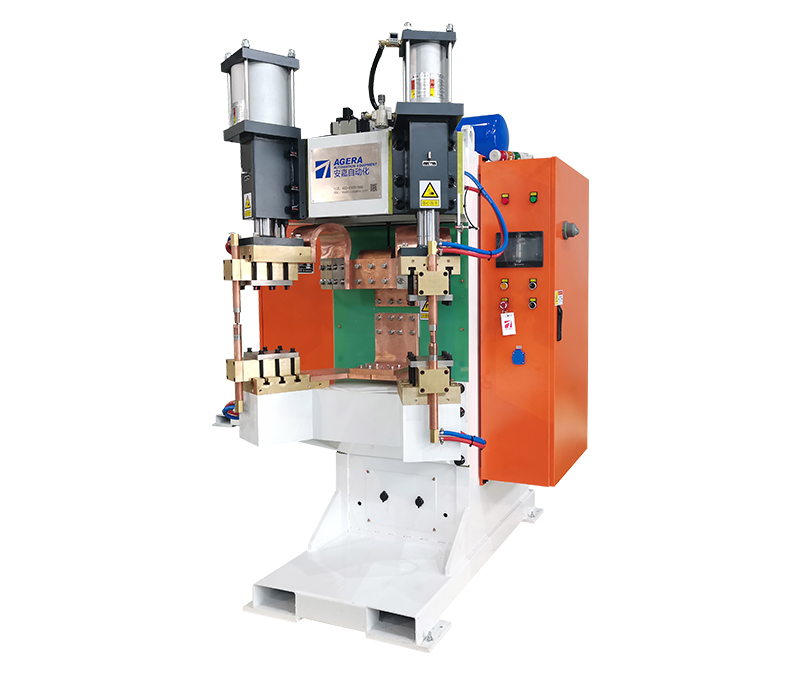
- Water Cooling System: Water cooling systems in nut welding machines utilize water as a coolant to dissipate heat generated during welding. The system typically consists of a water pump, water reservoir, cooling channels, and water-cooled electrodes. During welding, water is circulated through the cooling channels, absorbing heat from the electrodes and other components, and then expelled to an external cooling source or a heat exchanger to dissipate the accumulated heat. Water cooling systems are highly effective in maintaining consistent temperatures and preventing overheating, especially during prolonged or high-intensity welding operations. They help to extend the lifespan of the electrodes and other critical components by keeping them within the recommended temperature range.
- Air Cooling System: Air cooling systems in nut welding machines utilize forced airflow to cool the equipment. The system includes fans or blowers that circulate ambient air around the welding components, dissipating heat through convection. Air cooling systems are typically used in lighter-duty or intermittent welding applications where water cooling may not be necessary. They provide a cost-effective cooling solution and are relatively easier to install and maintain compared to water cooling systems. However, air cooling systems may have limitations in managing high heat loads or maintaining precise temperature control compared to water cooling.
Benefits of Cooling Systems in Nut Welding Machines:
- Heat Dissipation: Both water cooling and air cooling systems effectively dissipate the heat generated during welding, preventing equipment overheating and ensuring stable welding performance.
- Extended Equipment Lifespan: By maintaining optimal operating temperatures, cooling systems help prolong the lifespan of critical components such as electrodes, transformers, and electronic circuitry.
- Improved Weld Quality: Proper cooling reduces the risk of thermal distortion, allowing for more precise and consistent welds with minimized defects.
- Enhanced Productivity: Cooling systems enable longer continuous welding cycles by effectively managing heat, thereby increasing productivity and reducing downtime due to equipment overheating.
Water cooling and air cooling systems are essential components in nut welding machines. They provide effective heat dissipation, prolong equipment lifespan, improve weld quality, and enhance productivity. The selection of the appropriate cooling system depends on factors such as the intensity and duration of welding operations, equipment specifications, and cost considerations. By implementing suitable cooling systems, manufacturers can ensure the optimal performance and longevity of their nut welding machines.