Resistance spot welding is a widely used method for joining metal components in various industries. One of the critical components of a resistance spot welding machine is its drive mechanism, which plays a crucial role in controlling the welding process. In this article, we will provide an overview of the different drive mechanisms used in resistance spot welding machines.
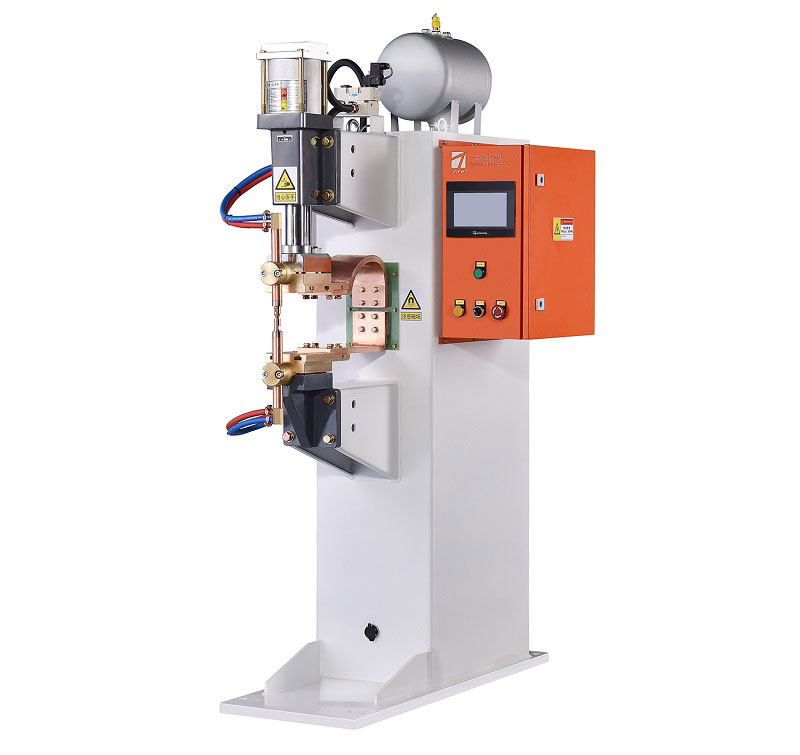
- Pneumatic Drive Mechanism: Pneumatic drive mechanisms are commonly found in smaller and portable spot welding machines. These machines use compressed air to control the welding force and electrode movement. When the operator initiates the welding process, the pneumatic system activates, applying the required force to the electrodes. This mechanism is simple and cost-effective, making it suitable for lightweight applications.
- Hydraulic Drive Mechanism: Hydraulic drive mechanisms are often employed in medium to large-scale resistance spot welding machines. They use hydraulic fluid to generate the force needed for welding. Hydraulic systems can deliver precise control over the welding force and electrode movement, making them suitable for applications where consistent and accurate welds are essential.
- Servo-Electric Drive Mechanism: In recent years, servo-electric drive mechanisms have gained popularity due to their high precision and flexibility. These systems utilize electric motors and controllers to precisely control the welding force, electrode movement, and welding current. Servo-electric systems can be programmed for various welding profiles, making them ideal for applications with complex welding requirements.
- Mechanical Drive Mechanism: Mechanical drive mechanisms are less common in modern resistance spot welding machines but are still used in some older models. These systems rely on mechanical linkages and cams to control the electrode movement and force. While they may lack the precision of pneumatic, hydraulic, or servo-electric systems, they are robust and durable.
- Electromagnetic Drive Mechanism: Electromagnetic drive mechanisms are relatively rare and are typically found in specialized resistance spot welding machines. These systems use electromagnetic coils to control the welding force and electrode movement. They offer precise control and can be suitable for applications requiring rapid welding cycles.
In conclusion, the drive mechanism of a resistance spot welding machine is a critical component that directly impacts the quality and efficiency of the welding process. The choice of drive mechanism depends on factors such as the size of the machine, the required precision, and the specific application. Whether pneumatic, hydraulic, servo-electric, mechanical, or electromagnetic, each drive mechanism has its advantages and is selected based on the unique needs of the welding operation.