Regular inspection and maintenance are essential for ensuring the optimal performance and longevity of butt welding machines. In this article, we will discuss the importance of daily checks and provide a comprehensive guide on inspecting key components to detect potential issues early on. By incorporating a routine inspection into the welding process, operators can enhance safety, prevent downtime, and achieve consistent weld quality.
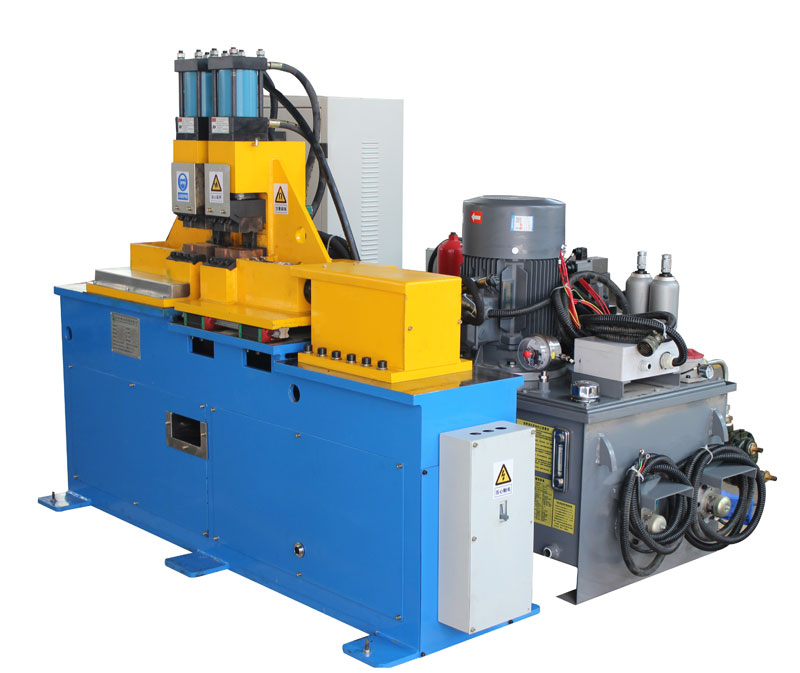
Introduction: Butt welding machines are critical tools in various industries, facilitating the fusion of metals through the application of heat and pressure. To ensure their smooth operation and prevent unexpected breakdowns, regular daily inspections are crucial. Through systematic checks of key components, operators can identify potential problems and take proactive measures to maintain the equipment’s efficiency.
- Visual Inspection: The daily inspection starts with a thorough visual examination of the entire welding machine. Operators should look for any signs of damage, loose connections, or abnormalities in the exterior structure. Pay special attention to electrical cables, cooling system hoses, and any visible fluid leaks.
- Electrical Components: Verify that all electrical components, such as switches, buttons, and indicators, are functioning correctly. Check the power supply, circuit breakers, and fuses to ensure they are secure and operating within the specified parameters.
- Cooling System: Inspect the cooling system, including water reservoirs, pumps, and hoses, to ensure proper functioning. Look for any obstructions or signs of leakage that may affect the cooling efficiency.
- Clamping Mechanism: The clamping mechanism is crucial for holding the workpieces firmly during the welding process. Inspect clamps, jaws, and alignment guides for wear, damage, or misalignment, as these issues can impact weld quality.
- Welding Electrodes: Check the condition of welding electrodes and ensure they are clean, sharp, and securely fastened. Replace any worn or damaged electrodes promptly to maintain consistent weld quality.
- Pressure System: Inspect the pressure system, including cylinders and pressure regulators, to confirm that they are in good working condition. Proper pressure control is essential for achieving accurate and reliable welds.
- Welding Controls: Verify the functionality of the welding controls, including current, voltage, and timer settings. Ensure that the settings match the welding requirements for the specific workpiece.
- Safety Features: Test all safety features, such as emergency stop buttons and interlock systems, to guarantee their immediate responsiveness in case of any safety hazard.
Daily inspections are an integral part of the preventive maintenance routine for butt welding machines. By conducting systematic checks of critical components, operators can detect potential issues early on and address them promptly, reducing the risk of equipment failure and improving overall safety and productivity. Incorporating daily inspections into the welding process helps ensure that the butt welding machine operates at its peak performance, delivering high-quality welds consistently.