Nut projection welding machines are widely used in industrial applications to join nuts and other components with high precision and efficiency. To enhance productivity and streamline the welding process, many manufacturers incorporate automatic feeding systems into their nut projection welding machines. In this article, we will provide an overview of automatic feeding systems for nut projection welding machines, highlighting their features and benefits.
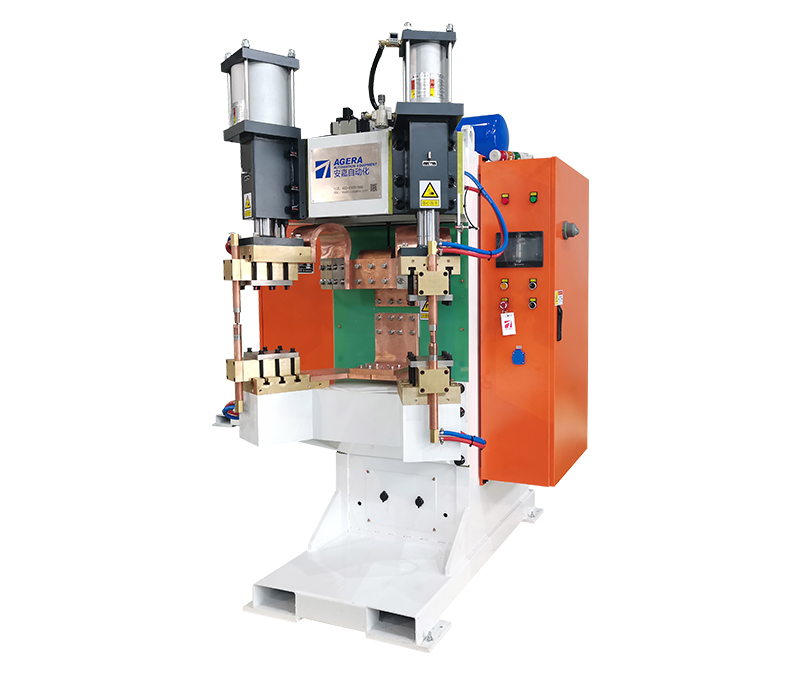
- Enhanced Efficiency: Automatic feeding systems eliminate the need for manual feeding of nuts into the welding machine. With automated feeding, nuts are supplied to the welding machine in a continuous and controlled manner, ensuring a consistent workflow and reducing downtime. This enhances overall production efficiency and throughput.
- Precise Nut Placement: Automatic feeding systems are designed to accurately position and orient nuts for welding. They employ mechanisms such as vibratory bowls, feed tracks, or rotary systems to align and deliver nuts to the welding area. This precise nut placement ensures proper alignment with the welding electrodes, resulting in high-quality and reliable welds.
- Versatile Compatibility: Automatic feeding systems are designed to accommodate a wide range of nut sizes and types. They can be easily adjusted or customized to handle various nut shapes, thread sizes, and materials. This versatility allows manufacturers to use the same welding machine for different nut welding applications, reducing the need for multiple setups or equipment.
- Integration and Synchronization: Automatic feeding systems are seamlessly integrated with the nut projection welding machine, forming a synchronized production line. They are typically equipped with sensors and controls to ensure smooth operation and synchronization with the welding process. This integration minimizes the risk of misfeeds or misalignments, enhancing the overall reliability and accuracy of the welding operation.
- Safety and Ergonomics: Automated feeding systems improve workplace safety and ergonomics by reducing manual handling of nuts. Operators are less exposed to potential hazards associated with manual feeding, such as finger injuries or strain. Additionally, ergonomic considerations are taken into account during the design of feeding systems to facilitate easy access, maintenance, and adjustment.
- Monitoring and Control: Advanced automatic feeding systems may incorporate monitoring and control features. They can be equipped with sensors and software to detect and rectify issues such as jamming, misfeeds, or insufficient nut supply. Real-time feedback and data collection enable operators to monitor the feeding process and make necessary adjustments for optimal performance.
Automatic feeding systems play a vital role in enhancing the efficiency, precision, and safety of nut projection welding machines. By automating the nut feeding process, manufacturers can achieve consistent and reliable welds, reduce manual labor, and improve overall productivity. With their versatility, integration capabilities, and monitoring features, automatic feeding systems are a valuable addition to nut projection welding machines in various industrial applications.