The quality of welds produced by butt welding machines is influenced by various intrinsic factors that lie within the welding process itself. Understanding these internal elements is crucial for welders and professionals in the welding industry to achieve superior weld quality. This article explores the intrinsic factors that can impact welding quality in butt welding machines, offering insights into how to optimize these elements for successful welding outcomes.
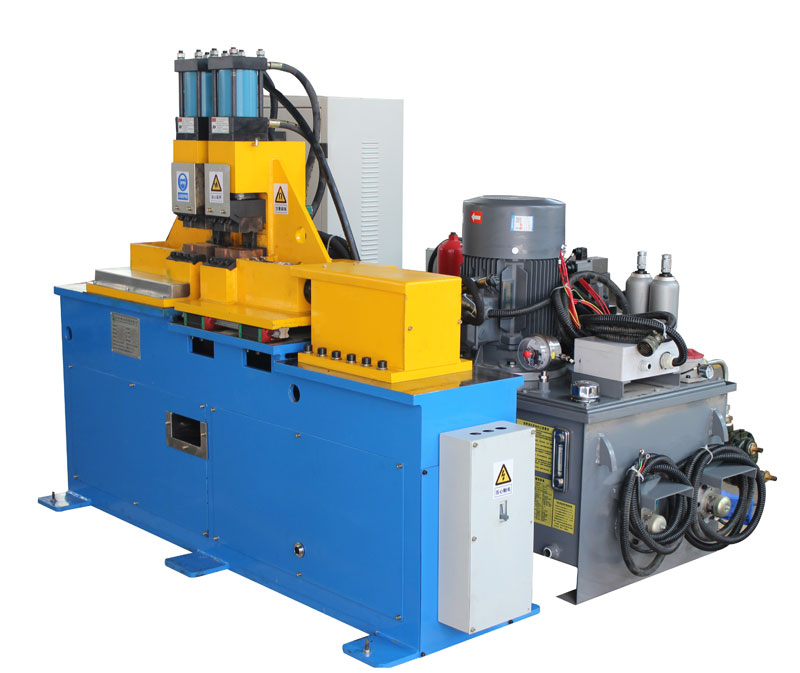
- Welding Parameters: One of the key intrinsic factors is the selection and control of welding parameters, including welding current, voltage, welding speed, and heat input. Properly adjusting these parameters ensures adequate fusion, penetration, and overall weld integrity.
- Material Selection and Preparation: The choice of welding materials and their preparation play a vital role in welding quality. Using compatible materials and preparing the joint surfaces adequately influence the strength and durability of the weld.
- Electrode or Filler Material: The type and quality of the electrode or filler material used in the welding process can significantly affect the metallurgical properties of the weld. Selecting the appropriate electrode for the specific application is essential for achieving optimal results.
- Welding Technique: Different welding techniques, such as gas tungsten arc welding (GTAW), gas metal arc welding (GMAW), or shielded metal arc welding (SMAW), can impact the welding quality. Each technique requires specific skill and precision from the welder to achieve desired outcomes.
- Joint Design: The joint design, including the geometry and fit-up, influences the ease of welding and the mechanical strength of the final weld. Proper joint design ensures uniform heat distribution and full fusion.
- Welding Sequence: The sequence in which different parts of the joint are welded can affect residual stresses and distortion. Following a suitable welding sequence is vital for minimizing potential welding defects.
- Preheating and Post-Weld Heat Treatment (PWHT): Applying preheating or post-weld heat treatment can reduce residual stresses and improve the microstructure of the weld, leading to enhanced mechanical properties and overall welding quality.
- Operator Skill and Training: The skill level and training of the welder significantly impact welding quality. A well-trained and experienced welder can control intrinsic factors effectively and produce high-quality welds consistently.
Optimizing Intrinsic Factors: To enhance welding quality in butt welding machines, welders and professionals should focus on optimizing the intrinsic factors:
- Conduct thorough material selection and joint preparation to ensure compatibility and proper fit-up.
- Regularly calibrate and adjust welding parameters to match the specific welding application.
- Employ suitable welding techniques for the intended welding joint and material type.
- Implement preheating or post-weld heat treatment when necessary to improve weld properties.
- Emphasize welder training and skill development to maintain consistent welding quality.
In conclusion, intrinsic factors significantly influence welding quality in butt welding machines. Optimizing welding parameters, material selection, joint design, welding techniques, and operator skill is essential for achieving superior weld integrity and mechanical properties. By addressing these intrinsic elements, welders and professionals can elevate welding performance, consistency, and reliability. Emphasizing the significance of intrinsic factors supports advancements in welding technology and fosters a culture of excellence in the welding industry.