Ensuring the quality of nut spot welding is crucial to guarantee the structural integrity and reliability of welded joints. Various inspection methods are employed to evaluate the weld quality, detect defects, and verify compliance with industry standards. This article explores different techniques and procedures used for inspecting nut spot welding and assessing weld integrity.
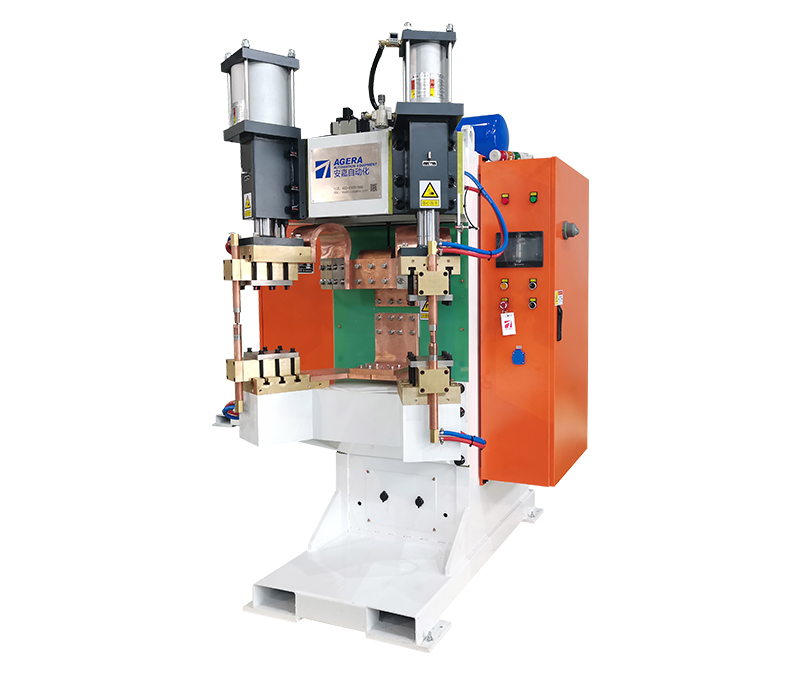
- Visual Inspection: Visual inspection is the most fundamental method for examining weld quality. It involves a visual examination of the welded joint to identify any visible defects, such as incomplete fusion, porosity, cracks, or improper weld size. Skilled inspectors assess the overall appearance of the weld and compare it against established acceptance criteria to determine if the weld meets the required standards.
- Dimensional Measurement: Accurate dimensional measurements are essential to ensure the weld joint conforms to design specifications. Using specialized tools, inspectors measure various dimensions of the weld, such as weld size, weld pitch, and weld length. Any deviations from the specified dimensions can indicate potential quality issues or process variations that may affect the weld’s performance.
- Destructive Testing: Destructive testing methods involve removing a sample or section of the weld joint for examination and evaluation. Common destructive tests for nut spot welding include tensile testing, bend testing, and microstructural analysis. These tests provide insights into the weld’s mechanical properties, including strength, ductility, and structural integrity.
- Non-Destructive Testing (NDT): Non-destructive testing methods are employed to assess the integrity of the weld without causing any damage. NDT techniques commonly used for nut spot welding inspection include ultrasonic testing, eddy current testing, and radiographic testing. These methods can detect internal defects, such as cracks, porosity, or incomplete fusion, ensuring the weld meets the required quality standards.
- Ultrasonic Time-of-Flight Diffraction (TOFD): TOFD is a specialized ultrasonic testing technique that provides accurate defect detection and sizing. It uses high-frequency sound waves to detect and characterize internal flaws in the weld, such as lack of fusion, cracks, or voids. TOFD offers reliable results and can be used for both manual and automated inspection processes.
Inspecting the quality of nut spot welding is essential to ensure weld integrity and reliability. Visual inspection, dimensional measurement, destructive testing, non-destructive testing, and specialized techniques like TOFD are valuable tools for assessing weld quality and detecting defects. By employing these inspection methods, manufacturers and inspectors can verify that the welds meet the required standards and specifications, ensuring the overall quality and performance of nut spot welding in various applications.