Capacitor discharge welding machines are known for their unique welding principle and distinct characteristics that make them a valuable tool in various welding applications. This article provides a comprehensive overview of the working principle, process characteristics, and advantages of capacitor discharge welding machines.
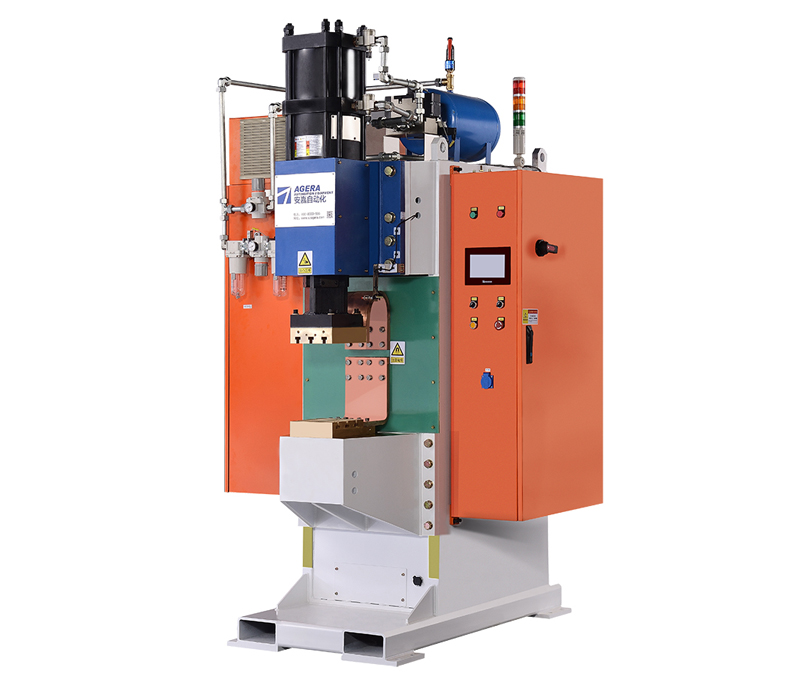
Capacitor discharge welding machines operate on a fundamentally different principle compared to traditional continuous welding methods. This principle, combined with specific characteristics, results in a versatile and efficient welding process. Let’s delve into the details:
Working Principle: Capacitor discharge welding relies on the rapid discharge of electrical energy stored in capacitors. When the welding process is initiated, the energy stored in the capacitors is released in a controlled manner through the welding electrode tips. This discharge creates a high-intensity electric arc between the workpieces, generating heat that leads to localized melting and subsequent fusion of the metals.
Process Characteristics:
- Precise Energy Delivery: Capacitor discharge welding offers precise control over energy delivery. This enables the creation of consistent and accurate welds, making it suitable for applications where precision is paramount.
- Minimal Heat Input: The short duration of the welding arc results in minimal heat input into the workpieces. This characteristic is beneficial for preventing distortion and minimizing the heat-affected zone, particularly in thin or heat-sensitive materials.
- Quick Solidification: The rapid energy release leads to quick fusion and solidification of the welded joint. This reduces the chances of metallurgical changes and ensures strong and reliable welds.
- Dissimilar Material Welding: Capacitor discharge welding is effective for joining dissimilar materials, as the rapid heating and cooling cycles mitigate the risk of intermetallic compounds forming between the metals.
- Limited Deformation: The controlled energy release contributes to minimal material deformation, making it suitable for applications where distortion is a concern.
- Reduced Post-Weld Cleanup: Due to the precise heat input, capacitor discharge welds often require less post-weld cleanup or finishing compared to other welding methods.
Advantages:
- Energy Efficiency: Capacitor discharge welding utilizes stored electrical energy efficiently, reducing overall energy consumption.
- Safety: The intermittent welding arc reduces the risk of electrical shock, enhancing operator safety.
- Micro-Welding Capabilities: The controlled energy release allows for micro-welding applications that demand precision and accuracy.
- Versatility: Capacitor discharge welding is suitable for a wide range of materials and joint configurations.
The working principle and characteristics of capacitor discharge welding machines make them a compelling choice for applications requiring precision, minimal heat input, and strong welds. Their ability to control energy delivery, ensure quick solidification, and accommodate dissimilar materials positions them as a valuable asset in various industries. The advantages of energy efficiency, enhanced safety, and micro-welding capabilities further highlight their importance in modern welding processes.