Welding round pipes using butt welding machines requires specific techniques and considerations to ensure strong and reliable welds. Understanding the process of welding round pipes is essential for welders and professionals in the welding industry to achieve precise and high-quality welds. This article provides a comprehensive guide on how to weld round pipes using butt welding machines, emphasizing key steps and best practices for successful welding outcomes.
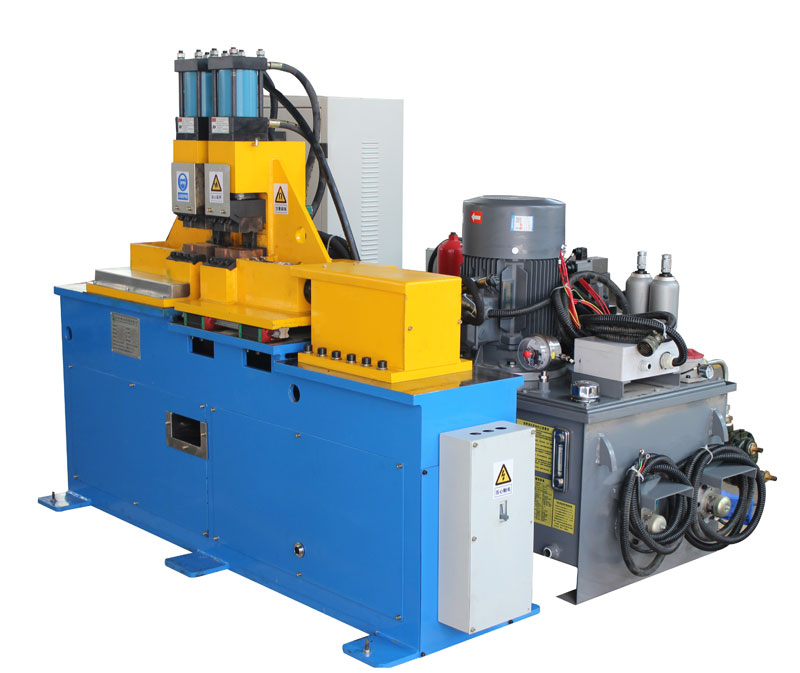
- Preparation: Before starting the welding process, thoroughly clean the surfaces of the round pipes to remove any dirt, oil, or contaminants. Proper cleaning ensures good fusion and minimizes the risk of defects in the weld.
- Fit-up and Alignment: Ensure accurate fit-up and alignment of the round pipes before welding. Proper fit-up is crucial to achieve uniform welds and avoid irregularities along the joint.
- Welding Parameters: Select appropriate welding parameters, including welding current, voltage, and electrode withdrawal speed, based on the pipe material, thickness, and joint design. Adjust the parameters to match the specific welding requirements for round pipe welding.
- Tack Welding: Use tack welds to temporarily secure the pipes in their desired position before the final welding. Tack welding helps maintain proper alignment during the welding process.
- Butt Welding Machine Setup: Set up the butt welding machine for round pipe welding, ensuring the machine is calibrated and aligned correctly. Verify that the welding electrode is properly positioned to achieve optimal weld bead formation.
- Welding Sequence: Start the welding sequence by positioning the welding electrode at the joint’s centerline and initiating the welding current. Maintain a steady electrode withdrawal speed to achieve consistent weld bead appearance.
- Control of Heat Input: Control the heat input during welding to prevent overheating and distortion of the round pipes. Proper heat control ensures uniform fusion and maintains the pipe’s original properties.
- Welding Technique: Adopt a suitable welding technique, such as semi-automatic or fully automatic, depending on the project’s scale and complexity. Maintain a stable arc and avoid interruptions to achieve smooth and continuous welds.
- Post-Weld Inspection: After completing the welding process, conduct a post-weld inspection to assess the quality of the round pipe welds. Visual inspection, dimensional measurements, and non-destructive testing can be employed to verify the weld integrity.
In conclusion, welding round pipes using butt welding machines requires careful preparation, accurate fit-up, and proper welding parameters. Tack welding, butt welding machine setup, control of heat input, and welding technique are crucial aspects to ensure successful welding outcomes. By following best practices and adhering to proper welding procedures, welders and professionals can achieve precise and high-quality welds in round pipes. Emphasizing the importance of proper preparation and welding techniques contributes to the optimization of round pipe welding and supports advancements in welding technology in various industrial applications.