In today’s rapidly evolving manufacturing industry, efficiency is the key to success. Every step of the production process should be optimized to maximize productivity, and nut spot welding machines play a crucial role in achieving this goal. In this article, we will explore how to use nut spot welding machines to enhance production efficiency.
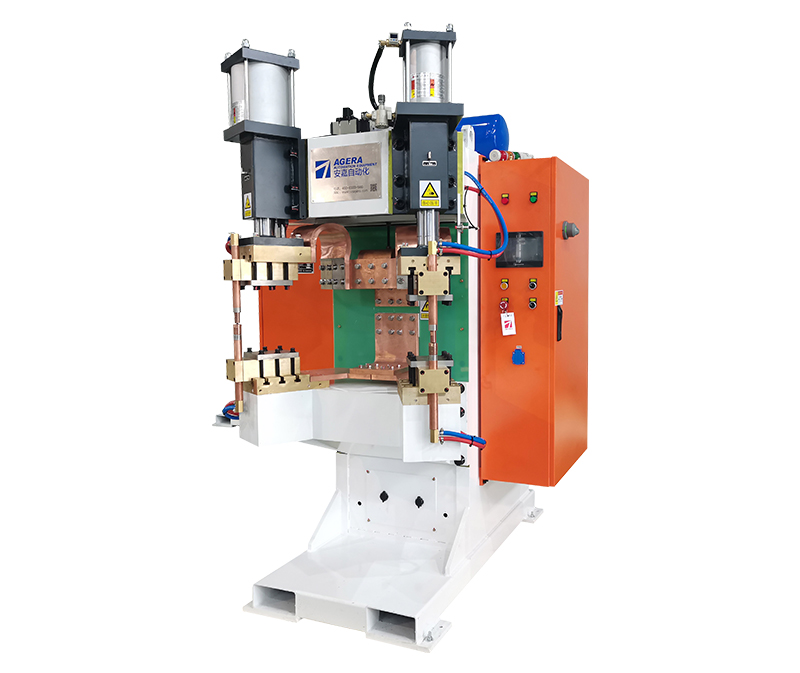
Understanding Nut Spot Welding Machines:
Before delving into ways to improve production efficiency, it’s essential to understand what nut spot welding machines are and how they function. These machines are designed to join nuts to various materials, such as metal sheets, through the process of resistance spot welding.
The basic operation involves placing the nut on the workpiece, aligning it correctly, and then using the welding machine to create a strong and durable weld. It’s a common technique in automotive and construction industries, where secure fastening is crucial.
Tips to Enhance Production Efficiency:
- Proper Machine Setup: Start by ensuring that the nut spot welding machine is correctly set up. This includes selecting the right welding parameters, such as welding current, time, and electrode force, depending on the materials and nut sizes you’re working with. A well-configured machine minimizes the chances of errors and reduces the need for rework.
- Quality Materials: Use high-quality nuts and materials. The strength and durability of the final weld depend on the materials being used. High-quality materials will result in a more reliable and robust product.
- Consistent Welding Technique: Train your operators to use a consistent and precise welding technique. This reduces the variability in the welding process, leading to higher-quality welds and fewer defects.
- Regular Maintenance: Keep the nut spot welding machine in optimal condition through regular maintenance. This includes cleaning, inspecting electrodes, and replacing them when necessary. A well-maintained machine is less likely to break down, causing costly downtime.
- Automate Where Possible: Automation can significantly enhance production efficiency. Consider using robotic systems for tasks that are repetitive and require high precision. Robots can work around the clock without fatigue, ensuring consistent quality and increased output.
- Quality Control: Implement a robust quality control process. This involves inspecting the welds regularly to catch defects early. If defects are detected, they can be corrected before they escalate, saving both time and resources.
- Training and Skill Development: Invest in the training and skill development of your operators. Well-trained personnel are more efficient and produce higher-quality welds.
- Data Monitoring and Analysis: Implement data monitoring and analysis tools to track machine performance and identify areas for improvement. Data-driven decisions can lead to more efficient operations.
- Efficient Workflow: Organize the workspace for efficient workflow. This includes the layout of the machines, material storage, and the movement of workers. A streamlined workflow can significantly reduce production time.
- Energy Efficiency: Consider the energy consumption of your nut spot welding machines. Implement energy-efficient practices and equipment to reduce operational costs.
In conclusion, nut spot welding machines are valuable tools in the manufacturing process. By implementing the tips mentioned above, you can enhance production efficiency, reduce costs, and produce high-quality products. In an industry where every minute and every resource counts, optimizing your nut spot welding process is a step in the right direction.